As more businesses adopt and grow their fleets of automated guided vehicles (AGVs) and autonomous mobile robots (AMRs), the need to be able to mix and match robot brands - called interoperability - is becoming increasingly clear.
Drivers of AGV/AMR interoperability
There are many different reasons why a company might require multiple brands of AGV or AMR on-site. These include:
- Single Supplier Limitations: Following an initial AGV rollout, a company might decide to automate further processes but find that the supplier of its original AGV/AMR vehicle does not offer models suited to these other tasks. Therefore, the need to bring in a second supplier.
- Adding New Vehicles to Existing: A company might have some existing/legacy AGVs or AMRs in use but is now looking to expand its automation program (or replace some of its existing fleet) by bringing in new, different brand vehicles. Thus, the need for these two sets of systems to work together.
In addition, enterprise-level buyers such as large manufacturers with multiple production sites, are increasingly thinking ‘platform first, vehicles second’. In other words, these organizations are looking to standardize their AGV and AMR operations around a single core technology, typically a fleet management software product, but with as few limitations on vehicle choices as possible. The dream: one fleet manager, rolled out globally, that can integrate pretty much any brand of AGV or AMR (whether the vehicle is existing or new) into any fleet they desire.
If successful, this approach promises to be efficient (one software technology), flexible (maximum vehicle choice), and require minimum overheads, compared to working with different providers with different fleet management technologies in different markets.
What problems does interoperability solve?
Typically, each brand of AGV or AMR runs using its own dedicated mission and fleet management software. This software is used to schedule and manage vehicle missions, manage traffic and vehicle charging, and seamlessly integrate a site’s automated vehicle operation with the business’ existing on-site business software (e.g., WMS, ERP, MES).
However, the fleet managers of different vehicle brands have not traditionally been capable of natively communicating with each other.
For the increasing number of users who are deploying or evolving larger fleets, and increasingly require multiple types of vehicles from different vendors, this lack of fleet manager collaboration can vastly complicate matters. There are several reasons for this:
- The management of an overall AGV operation, and the installation of any new vehicles, is more complex and time-consuming when multiple fleet managers are involved.
- Since vehicles cannot share the same virtual routes, they often need to run on different paths around a site, requiring significantly more space.
- Custom programming is required to handle any points where vehicles need to cross paths.
- Staff must learn how to use different fleet management software programs.
- Companies also need to manage relationships, support, and contracts with two or more different software suppliers.
- Multiple fleet manager software licenses likely cost more than just one (whether itemized or rolled into an AGV supplier’s integration/maintenance costs).
Interoperability, however, promises to sidestep these challenges. A company can run just one fleet manager software project, within which multiple brands of vehicle can operate, using just one set of virtual paths and with just one software program to learn and one supplier to deal with.
3 ways to achieve interoperability
Today there are three ways to achieve AGV/AMR fleet interoperability:
- Sharing spaces using interlocks to create what are effectively ‘virtual traffic lights’.
- By adopting one (or more) of the industry’s evolving fleet interoperability standards.
- By choosing a fleet management platform and related vehicle ecosystem that already natively supports multi-brand vehicle operation (without ruling out compatibility with those same interoperability standards).
Let’s explore each of these three approaches in more depth.
1. Sharing spaces by using interlocks (virtual traffic lights)
An interlock is a programmed link between two different fleet managers that enables AGV/AMR traffic to deal with shared areas, such as crossings and particular sections of routes, smoothly. For every shared space, the different fleet managers concerned effectively ‘talk’ to each other to decide which vehicle has the right of way.
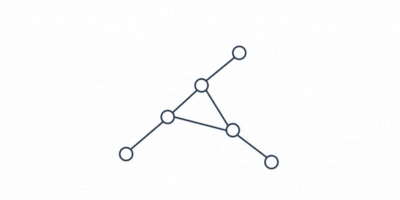
Take this example: AGV brand A is already installed on-site and a company now wants to add a second brand of vehicle to the operation. The integrator (usually the vehicle maker but maybe a third-party system integrator) would identify the sections in question and program a ‘handshake’ between the fleet managers at these locations.
In operation, a vehicle that is about to enter a shared section will notify any oncoming vehicle – via the programmed fleet manager interface – that it is coming, in turn blocking the shared path; the equivalent of a traffic light turning red to allow crossing traffic to pass. When the first vehicle clears the area, it will then unblock the path and the waiting vehicle will be notified; the equivalent of the traffic light turning green.
There are two key issues with the interlock approach:
- To carry out the basic programming required, an AGV’s integrator must have direct access to the second fleet manager supplier in order to collaborate and develop the handshake protocol. Unless the two companies are able (and willing) to work together, it will not be possible to create the interlocks required.
- The more shared sections there are, the more complicated, costly, and riskier using interlocks becomes. This may, in select cases, cause deadlocks that the two fleet managers cannot handle automatically.
2. Fleet management standards
Various organizations across different regions are also working on fleet management-level communication standards. These are solely designed to make it easy for different brands of AGV and AMR to work together seamlessly.
The most advanced standard to date is VDA 5050, which is driven by the German automotive industry in collaboration with VDMA Materials Handling and Intralogistics Association. VDA 5050 aims to enable compliant AGVs to work seamlessly together in one multi-brand fleet.
Newer still is the MassRobotics standard from the U.S. This focuses more on communication between AMRs themselves than their operations. There is also a Chinese standard in development, driven by the China Mobile Robot and AGV Industry Alliance (CMR), and the Open RMF interoperability standard out of California.
VDA 5050: A deeper dive
VDA 5050 is the most advanced standard today, however it is still quite basic in terms of the functionality it enables. The most recent version of the standard (V 2.0), for example, does not currently cover:
- Advanced traffic management
- Battery management
- Interactions with on-site equipment
- Multi-floor installations
When fully mature, VDA 5050 could bring significant value to the industry. However, it is expected to be at least two or three more years before it evolves from its current version to a final standard that can enable advanced functions such as those mentioned above.
A crucial point is this: while many AGV/AMR makers and third-party fleet manager providers claim ‘VDA 5050 compliance’, since the standard is not yet mature. Basing a fleet a developing standard today will very likely create additional installation and operational challenges in the future, which users will have to face on their own.
More specifically, vehicle integrators will likely need to custom develop software on top of the VDA 5050 base, developing their own ‘dialects’ to provide the advanced functionality that is not yet covered by the standard itself. And by doing so, end customers in turn may face the prospect of costly future upgrades to ensure their operations remain VDA-compliant when the standard is finally complete.
> Find out more about the VDA 5050 standard.
Even when fleet management standards are mature, they might not be the right approach for every company. To reach the broadest number of potential users, the functionality these standards offer may end up being built around the lowest common denominator, which might compromise vehicle speeds and site efficiency, and therefore stand in the way of optimization.
Interoperability standards: The support question
More rarely discussed than even the need for ‘dialects’ is the tricky future support question.
If a company has several AGV suppliers, and potentially a third-party fleet manager provider too, who will install and integrate what? Who will the customer call if and when something goes wrong? If there is a vehicle deadlock and the AGV operation stops, what then?
Some specific questions to consider include:
- Who will commission (install) the different brands of vehicle?
- Which software tool will be used to program the missions for the different brand vehicles?
- How will the characteristics of the different vehicles be defined?
- Which company will guarantee that AGV 1 and AGV 2 reach the exact same position (such as a pick or drop point)?
- Who will be responsible (e.g. at the end of the phone) if AGV 1 and AGV 2 become deadlocked during operation?
3. Interoperable ‘ANT driven’ fleets run by ANT server software
BlueBotics’ fleet control software, called ANT server, offers advanced mission and fleet management functionality for vehicles driven by BlueBotics’ own ANT navigation technology. The result is that over 150 models of different-brand AGVs and AMRs can be configured to work together seamlessly in a single fleet.
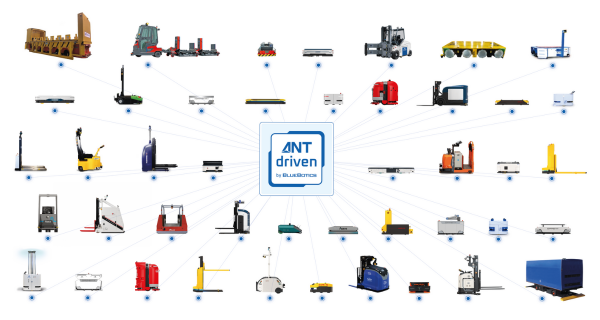
The functionality of ANT server covers, for example:
- Mission scheduling and management
- Traffic control
- Charging management
- Interfacing with on-site equipment (automatic doors, elevators etc.)
- Project simulation
- The ability to manage multi-floor installations
- Plus, a simple API for easy WMS/ERP/MES integration.
- Even outdoor operation is possible.
Effectively, the ANT platform offers all the final-stage functionality that VDA 5050 and similar standards promise, and more, only available today.
Watch a multi-brand ‘ANT driven’ fleet in action:
In addition, the team at BlueBotics are working on making ANT server compliant with all of the interoperability standards mentioned above. This will guarantee that companies can enjoy the best of both worlds: advanced multi-brand ANT driven fleets, with the potential for even wider expansion.
Interoperability in summary
As the number of automated vehicles being deployed continues to grow, and individual AGV/AMR projects become larger and more complex, vehicle interoperability will become more and more crucial.
If only a few AGVs or AMRs are involved, interlocks represent an inexpensive, reliable solution. However, projects involving several different vehicle models or brands will likely be larger, more complex, and therefore require more sophisticated management.
While mature interoperability standards will undoubtedly play a role in managing such complex installations, the goal of using these standards to manage such operations – at least without significant extra development and future compliance updates being required – remains several years away.
In the meantime, choosing a vehicle fleet based upon a natively interoperable fleet manager like ANT server – which will in future also be compliant with VDA 5050 and similar standards – can be an effective way to achieve a high-functioning yet flexible fleet that can adapt to a company’s changing needs.