In this article, we’ll take a closer look at the pros and cons of the different navigation systems driving AGVs, AMRs and automated forklifts today.
Physical paths: following lines and tags
The very first automated guided vehicles ran on rails. Vehicles that today follow physical lines and tags can be seen as direct descendants of this technology.
Line following AGV navigation
Line following AGVs are equipped with a special sensor capable of 'following' a physical line on (or under) the ground. This line could be magnetic tape, painted on the floor, or inductive wire that is physically embedded in the floor itself.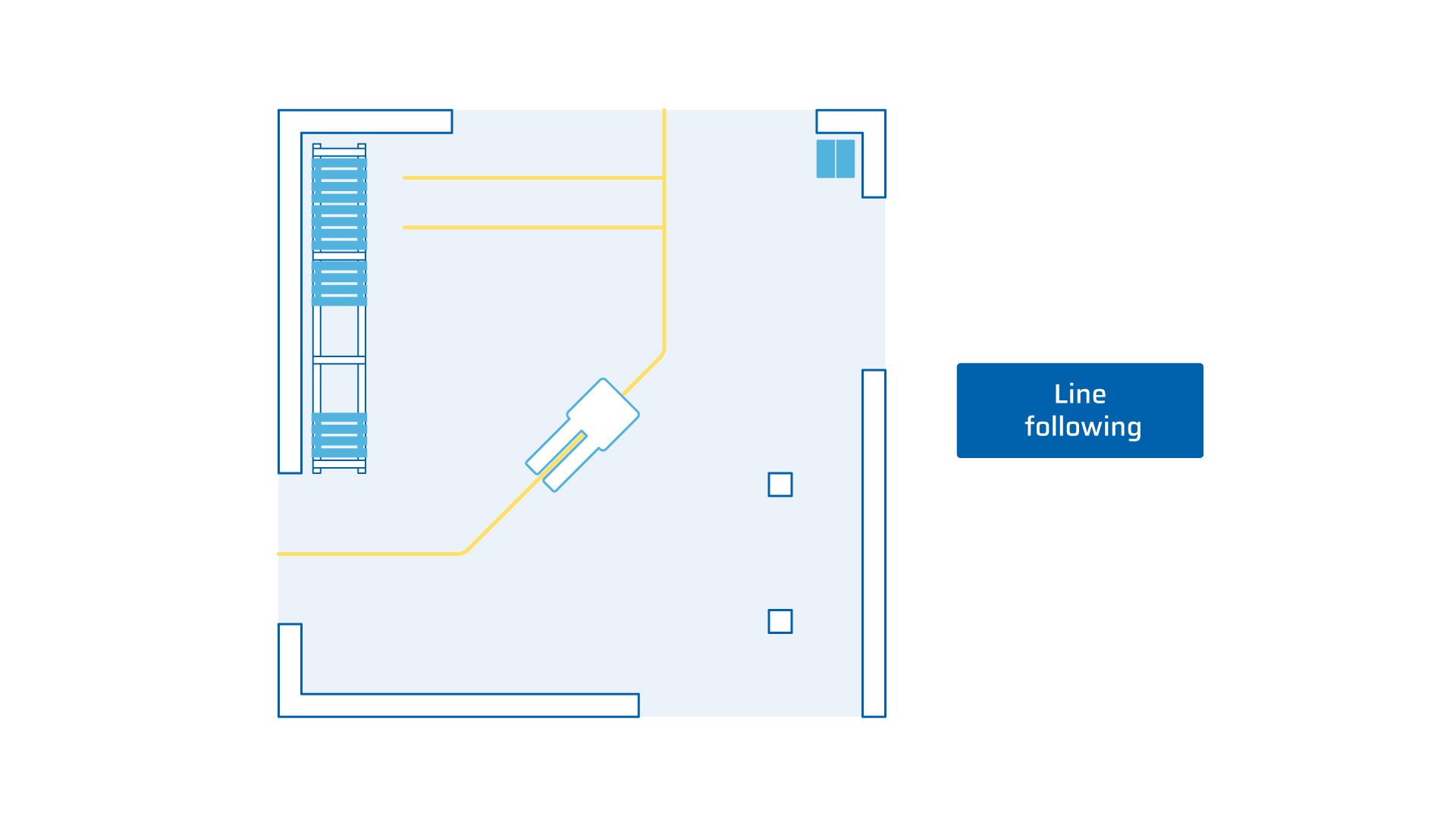
Tag following AGV navigation
Similar to line followers, tag following vehicles are equipped with a sensor (such as a camera or code reader) that allows them to follow a route that is defined by tags. These tags might be magnetic points embedded in the floor, or more commonly, QR or other types of codes.
Pros and cons of line & tag following vehicles
- PRO: Both of these AGV navigation technologies are highly reliable and very accurate.
- PRO: They are not affected by dynamic changes in the environment, such as the appearance or removal of pallets, materials, racking systems or other vehicles.
- CON: These systems are time-consuming and therefore can be expensive to install (embedding a physical line in the floor is especially disruptive), and this process will need to be repeated if routes need to change.
- CON: Magnetic tape, paint and tags/codes can also all suffer from wear and tear over time, leading to the risk of 'broken' routes and therefore vehicle errors.
- CON: Fleet management with line and tag following vehicles is difficult: one single AGV following physical lines or tags may work well, but getting multiple vehicles to work seamlessly together - for example, at crossings - can be highly problematic.
Laser and visual guidance
This next category of navigation uses lasers or cameras to calculate a vehicle's position in the environment. The paths followed however are virtual (or digital), not physical.
Laser triangulation
Laser-guided vehicles (or LGVs) calculate their position with the help of laser beams. These are fired around the environment using LiDAR laser scanners positioned on the vehicle and reflected back from carefully installed reflective targets. So long as a minimum of three targets can be 'seen' at any one time, the vehicle can calculate its position accurately and reliably. Therefore, the careful design of reflector locations is key.
Along with natural navigation, laser triangulation is one of the most popular AGV navigation methods used today.
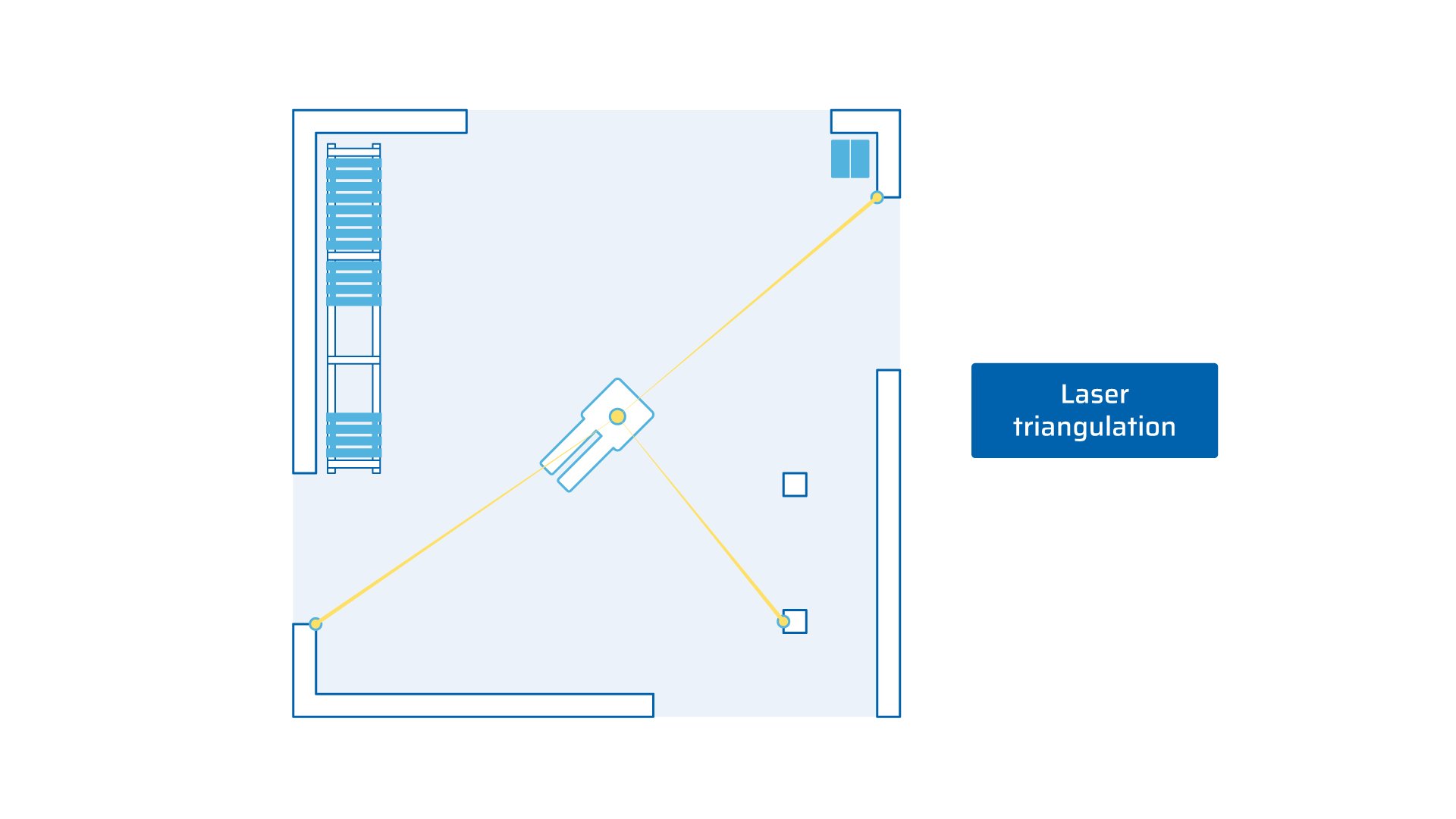
Laser guidance pros and cons
- PRO: Laser triangulation is reliable and highly accurate.
- PRO: Since a central server is used to manage vehicles following virtual routes, managing a fleet of multiple automated vehicles is effective and efficient.
- PRO: Since vehicle routes are digital, modifying these when an operation evolves is quick and simple. Unless that is, the locations of reflector installations need to be changed, which can be time consuming and expensive, since reflectors must be installed first by a technician and then their positions measured by a professional surveyor.
- CON: The process of installing LGVs (which includes designing reflector layouts, installing reflectors and then validating their position) can be time-consuming and expensive.
- CON: Since a vehicle's laser is generally placed on top - to maximize the number of wall-based targets it can 'see' - this means there are fewer types of LGVs available than there are vehicles driven by, for example, natural navigation. That's because there is nowhere on an underride or 'mouse' AGV for a triangulation laser to sit. While natural navigation can use the machine's ankle-height safety laser scanners to navigate, LGVs need that higher position to work effectively. This may not be a concern now. But if your organization's fleet requirements change in future and you need to grow your fleet, it would obviously be ideal if all your vehicles could run on the same navigation platform, such as ANT).
Vision guidance
AGVs that use vision guidance to get around use cameras to recognize features in the environment and calculate the vehicle's position.
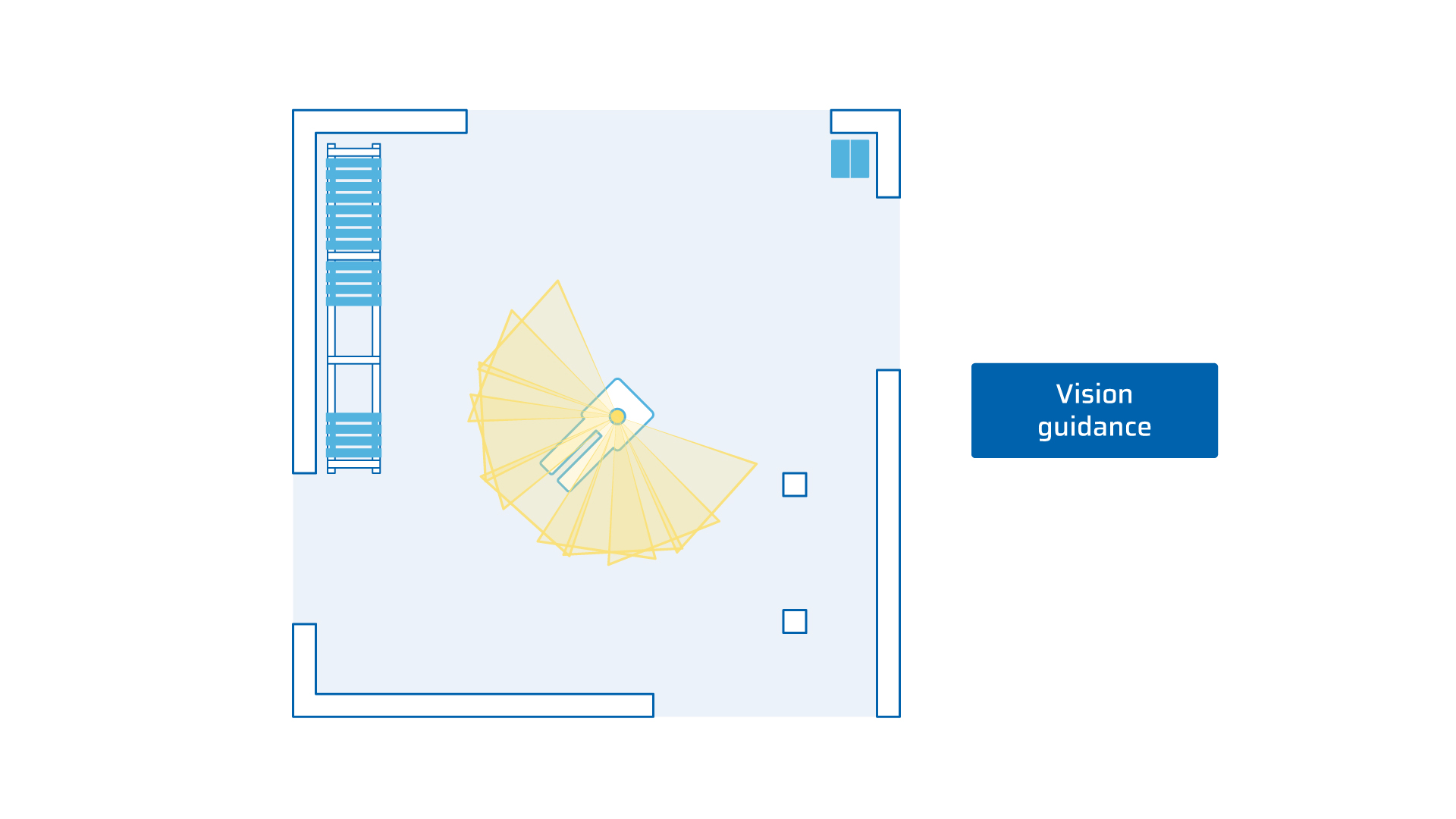
Vision guidance pros and cons
Vision guidance vehicles are quick and simple to install. No infrastructure changes are required.
However, the accuracy and reliability of vision-guided AGVs can be affected by changes in the environment and lighting conditions. The latter could be a particular concern if your site has inconsistent light conditions or if you are moving towards a lights-out operation.
Natural navigation
Natural navigation such as ANT (sometimes called free or contour navigation) is reliable, accurate, and its vehicles quick to install and modify. This approach uses permanent, static 'features' (or references) in the environment - such as walls, columns and fixed machinery - to calculate the vehicle's position.
However, not every natural navigation system works in the same way. In reality, two slightly different approaches exist:
- Scan matching (also called SLAM navigation)
- Feature matching (also called natural feature navigation).
Scan matching natural navigation
Vehicles that use scan matching natural navigation measure points in the environment using a laser scanner on the vehicle. Thousands of points are captured, and these are then matched with a grid-based reference map of the environment to calculate the vehicle's position (key to effective navigation).
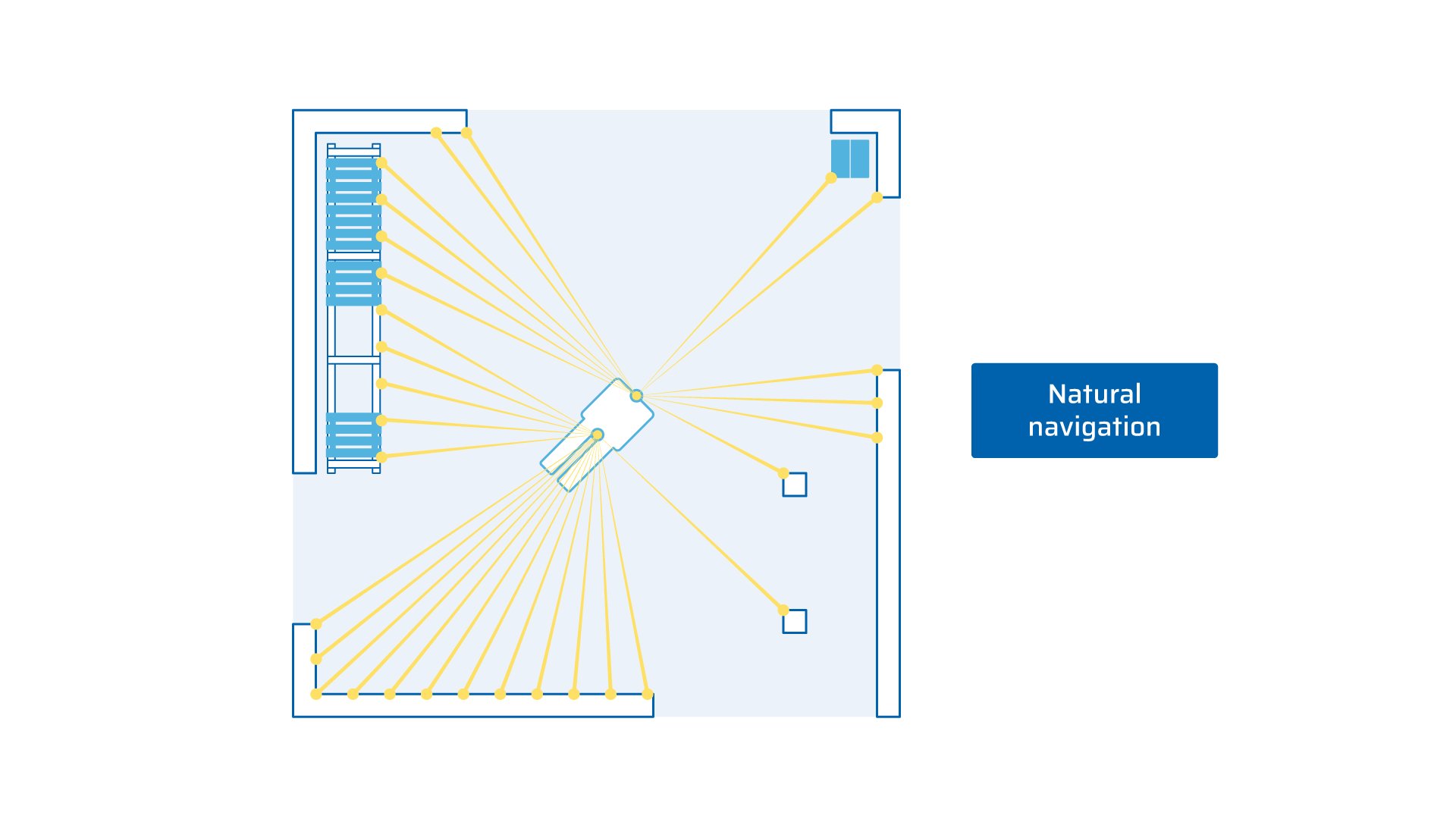
Scan matching pros and cons
- PRO: Scan matching vehicles are quick to install and modify.
- PRO: Since vehicle paths are virtual, fleet management via a central server is efficient.
- PRO: No permanent infrastructure changes are required. Occasionally, reflective stickers might need to be added – in areas with few visible natural features - but, unlike laser triangulation, these do not need to be validated by a professional surveyor.
- CON: Vehicles using scan matching navigation are more sensitive to changes in the environment (such as equipment and materials appearing or being moved) than vehicles that match features (see below). This sensitivity can lead to a vehicle’s accuracy and robustness being affected over time.
- CON: Vehicles that use scan matching often require an additional laser scanner to be installed high on the vehicle, to maximize the visibility of permanent features. This limits the number of vehicle types that are available based on this technology, in addition to raising costs.
Feature matching natural navigation (e.g. ANT natural feature navigation)
ANT natural feature navigation by BlueBotics is distinct from the natural navigation systems offered by other companies.
As with scan matching navigation, with natural feature navigation, the environment is measured with laser scanners (in this case usually a vehicle’s existing safety lasers). Permanent, static structures or ‘features’ in the environment are then matched with those on a reference map, allowing the vehicle to accurately calculate its position and navigate effectively.
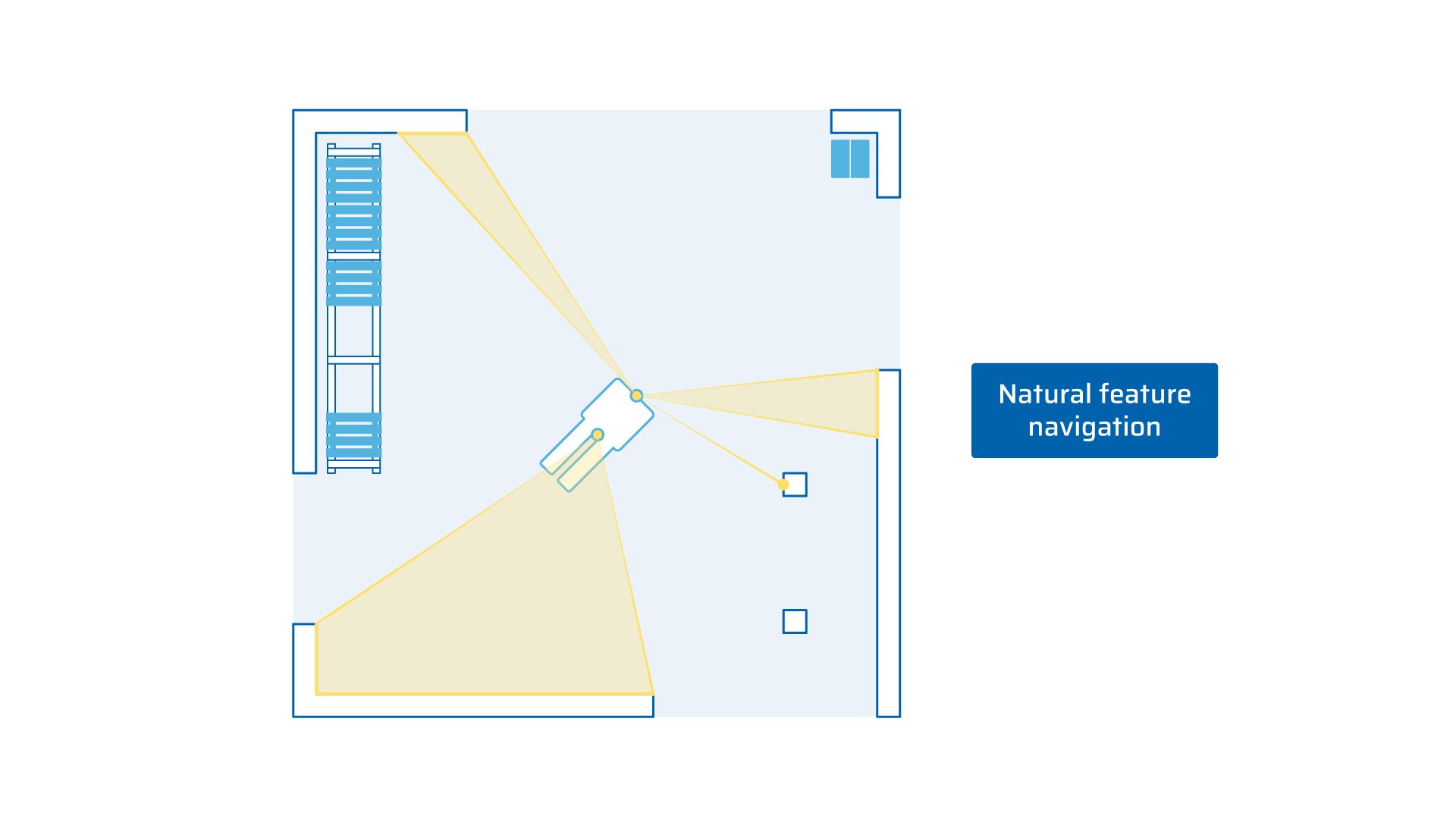
Natural feature navigation pros and cons
- PRO: Natural feature navigation is accurate and reliable.
- PRO: ANT driven vehicles are quick to install and modify, requiring minimal infrastructure changes (at most, a handful of reflective stickers).
- PRO: ANT driven vehicle installations are robust to environmental changes; vehicles can navigate even if less than 5% of an area's features are visible.
- PRO: Many ANT driven vehicles can be operated in a connected fleet using ANT server software. Users can even integrate different types and even brands of ANT driven vehicles in the same fleet. These vehicles can be run using ANT server software directly or via a company's existing business software (WMS, MES, ERP etc.).
- PRO: Because ANT navigation typically uses a vehicle's built-in laser safety scanners (which are located at ankle height), a wide range of vehicle options exist: from small “mouse” AMRs to cargo movers with payloads of several tons.
Comparing AGV navigation systems
Let’s look at the pros and cons of these different types of AGV navigation systems side by side.
Can you mix and match vehicles running on different navigation systems?
Suppose your ideal AGV operation features two or more different types of vehicles, which use different navigation systems. Can you run these vehicles on the same site?
Yes, in theory. But in practice, this is not straightforward. There are several challenges:
- Vehicle installations will need to be separate projects, meaning more expense and more time. Different configuration software packages will need to be used, with different integrators possibly on-site. Managing and synchronizing their work could be a challenge.
- Different fleet management systems are also likely to be needed in order to manage vehicles and their missions. Even if this just means different connections coming into your existing WMS, the different systems will likely use different commands and require extra staff training.
- Traffic management will be a challenge. It is unlikely that vehicles using two different navigation systems will be able to communicate natively. Getting them to “talk to each other” may take a lot of work, or it may not be feasible at all. Therefore...
- More physical space may be required. Vehicles that use different management systems are unlikely to be able to use the same lanes. Every type of vehicle may need its own dedicated paths (whether physical or virtual) around the site.
By contrast, many ANT driven vehicles are interoperable, meaning different brand vehicles with ANT inside can be run in one ANT server fleet (managed via your own business software if preferred). You can browse these interoperable vehicles using this site's Vehicle Finder (just check the 'multi-brand fleet' filter).
Which AGV navigation system is right for your business?
Carefully considering an AGV’s navigation system when making any vehicle investment could have a significant impact on the success of your automation project.
For reliability, accuracy, and ease of installation and modification, we believe that ANT by BlueBotics is the right choice. Whether you are starting with a small AGV operation on a single site, or planning an international automation project across multiple locations, ANT driven vehicles can ensure your business grows as efficiently as possible.