In this article, we’ll examine why natural navigation for AGVs is:
- Accurate (without requiring major, permanent changes to the environment)
- Repeatable over time
- Proven in industrial settings
What is natural navigation for AGVs?
Natural navigation (sometimes called free or contour navigation) is a type of automated guided vehicle technology. AGVs using natural navigation calculate their position (the key to accurate navigation) by “seeing” the environment through their laser scanners, rather than following physical lines on the ground or triangulating their position.
There are two main types of natural navigation for AGVs: scan matching and feature matching.
- Scan matching AGVs compare every part of the environment they “see” to a grid-based reference map. Also called SLAM navigation.
- Feature matching AGVs compare the permanent, static features in the environment they see (such as walls and pillars) to a feature-based map. This approach is used by ANT navigation.
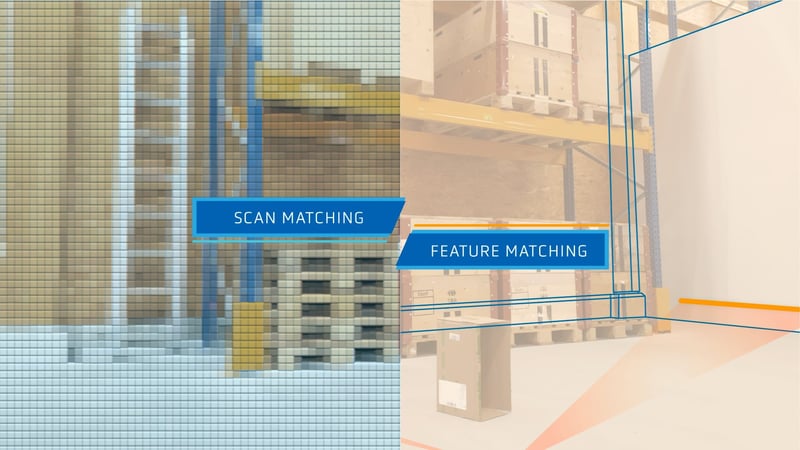
Both natural navigation technologies are reliable, but this article will focus mainly on ANT 'feature matching' navigation.
Accurate to within a centimeter or less
AGVs driven by ANT natural feature technology can achieve an accuracy of 1cm/1°. And do so again and again.
Accuracy to within a centimeter is accurate enough for the vast majority of industrial applications. (And in real-world situations, this precision can be optimized still further using bumpers and guides if needed.) It’s as accurate as a human would ever expect to be. But unlike most humans, AGVs never deviate from their programmed instructions.
ANT driven AGVs can reliably pick up and drop off loads, dock at recharging stations, and interact safely with human coworkers – all with human-level accuracy.
The Stöcklin Logistik video below features several picking, dropping and recharging examples, which show ANT's accuracy in action:
Accurate – without major changes to the environment
Unlike many other AGV navigation technologies, natural navigation does not require permanent changes to the environment.
Line and tag following technologies, for example, require tape or tags to be stuck to the floor, lines to be painted, or inductive wire/magnets to be installed in the floor itself. If changes to your AGV's routes are required later, modification can take time and money. Not to mention how materials that are stuck to the floor can become worn over time.
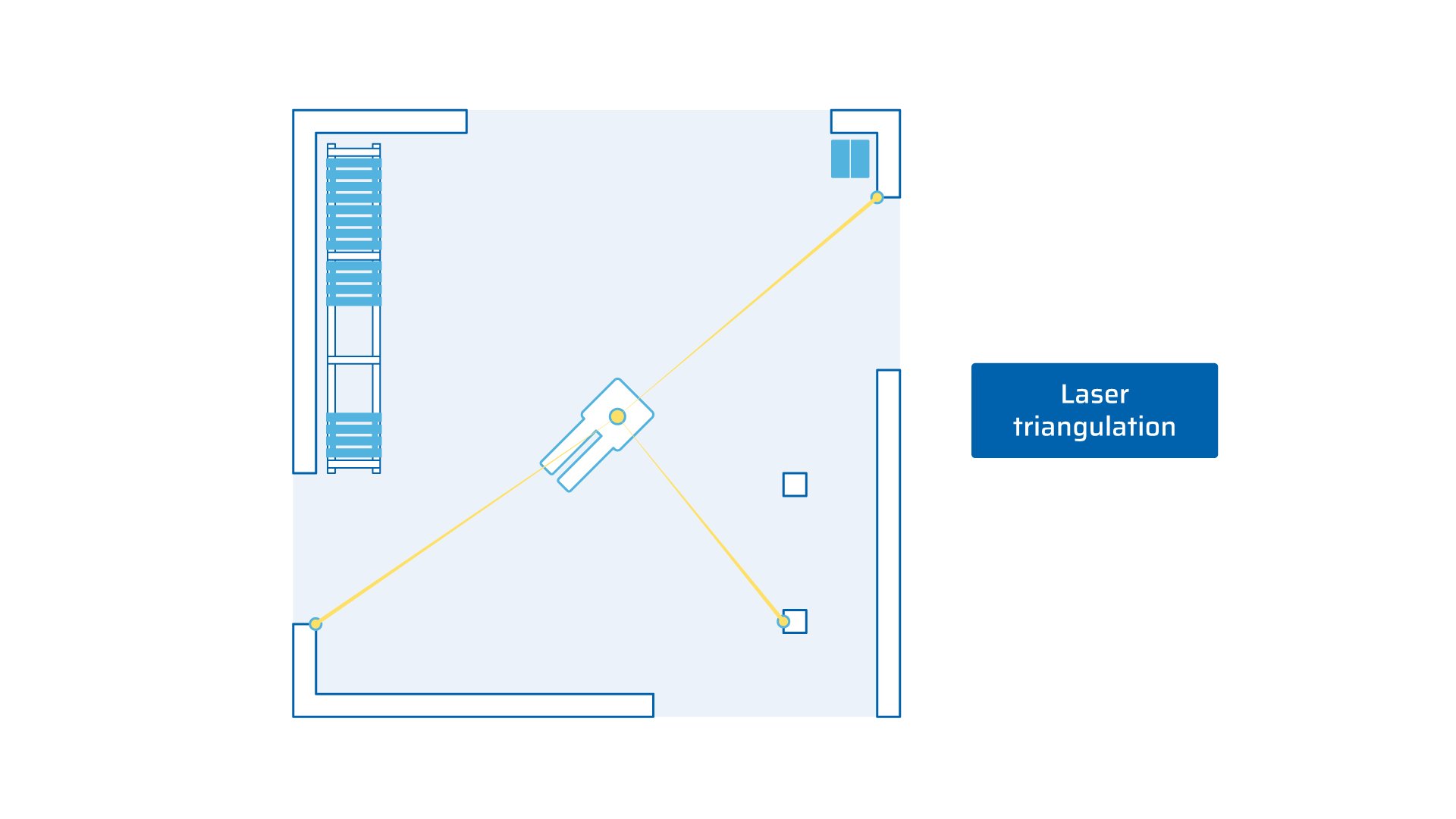
The most infrastructure changes an ANT driven vehicle might ever require is the addition of small reflective stickers, placed at ankle height, in areas of no 'natural' features. Unlike those reflectors used by laser triangulation, however, these stickers do not need to be professionally installed and may often not be required at all.
Reliable and repeatable
Achieving accurate results repeatedly is never easy, even with natural feature navigation, but with ANT it is possible.
Because ANT calculates a vehicle's position in its map by referencing distinct, static features in the environment (such as walls and pillars), and because this process ignores dynamic or temporary objects such as people and pallets, an ANT driven vehicle is able to calculate its position and operate accurately, every time.
What's more, an ANT driven vehicle only needs to see a small percentage of natural features at any one time (less than 5% of the environment) to navigate effectively.
Assuming the natural features on-site do not change (e.g. walls, columns or pieces of permanent machinery are not moved), there is no need for the vehicle’s reference map to be updated - even after years of operation.
Industry-proven results
The very first commercially installed ANT driven AGV (an EMS Group Paquito) was installed on-site in Italy in 2009. Today that vehicle has been replaced due to wear and tear, but the installation itself uses the exact same map, and the new vehicle navigates just as accurately as its predecessor did during its first day on the job.
Since then, vehicles driven by ANT technology have travelled over 10 million kilometers; that’s 250 times the circumference of the earth.
With this level of performance, it is no wonder that natural feature navigation technology is fast becoming the industry norm.
The right vehicle for your application
ANT natural feature navigation technology by BlueBotics can be used to drive numerous types of AGVs, automated forklifts and mobile robots - from obstacle avoiding AMRs and underride “mouse” AGVs, to larger counterbalanced forklifts and huge heavy unit load carriers designed to move payloads of 100 tons.
Whatever your application, there is probably an ANT driven vehicle to suit your application.