Unless the area in which your automated vehicles will work is 100% automated, it is inevitable they will encounter obstacles of some sort. From pallets and boxes to human coworkers, members of the public, and other vehicles – anything in front of an AGV or AMR's safety laser scanners should bring the vehicle to a stop.
That’s why it’s essential to have a plan to deal with these obstacles.
The vehicle's choice is simple: it will either stop and wait for the obstacle to be removed by a member of staff (what we can term 'virtual path following'), or it will dynamically plot a new route to its destination ('obstacle avoidance').
Obstacle avoidance: The difference between AGVs and AMRs
Generally speaking, the question of whether a vehicle uses virtual path following or obstacle avoidance is a simple way to determine whether it is an automated guided vehicle (AGV) or an autonomous mobile robot (AMR).
When faced with an obstacle:
- Virtual path following vehicles use collision avoidance: they stop and wait for the obstacle to be removed. This is most AGVs.
- Obstacle avoidance vehicles plot a dynamic route around the obstacle instead. AMRs that are driven by natural navigation almost always use this approach, plus some AGVs (such as those driven by ANT navigation) are also able to use this option.
In the case of vehicles that are driven by ANT navigation technology, distinctions based on navigation fall apart, since ANT driven vehicles can use either obstacle avoidance or virtual path following. In some cases, they might even use one mode in one area of a site, and the other in another area.
Virtual path following | Obstacle avoidance |
---|---|
Used by: AGVs |
Used by: AMRs, some AGVs driven by ANT |
When an obstacle is placed in its path... The vehicle stops and waits for the obstacle to be removed by trained human coworkers |
When an obstacle is placed in its path... The vehicle dynamically navigates around it before returning to its original path at the earliest opportunity |
Which is more efficient: obstacle avoidance or path following?
This depends on the working environment and your specific application.
In a busy, dynamic environment such as a shopping mall or airport, obstacle avoidance is preferred. After all, in such an environment, obstacles are inevitable and plentiful. And the vehicles that work in those spaces (such as Cleanfix cleaning robots or an automated airport check-in desk) are typically programmed not to move from A to B, but to cover as much of the surface area as possible; the manner in which they do this is less important.
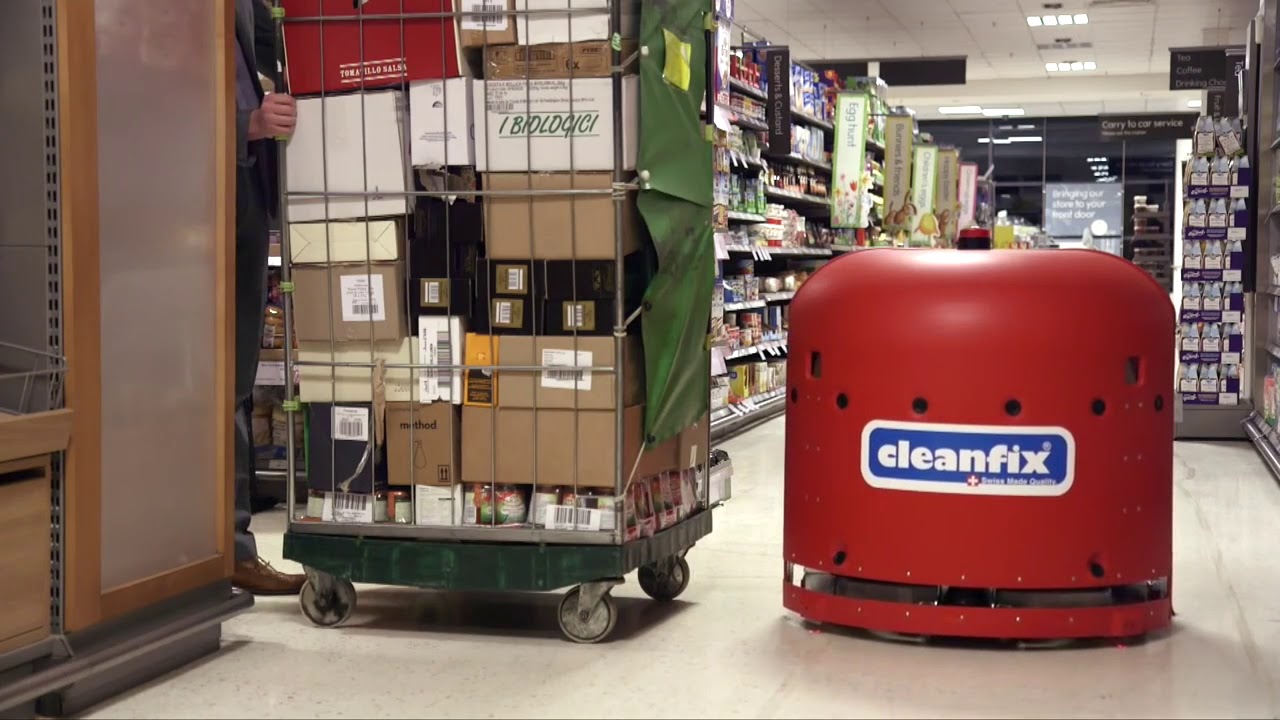
In a stricter, more controlled, and less dynamic environment, such as a production facility, however, path following is typically more efficient. This can seem counter-intuitive at first.
In such environments, time is money and staff are trained to optimize efficiency. If a vehicle stops and beeps, moving a pallet that is blocking its path should be quick and simple. Contrast this with a vehicle that uses obstacle avoidance. It will move around the blockage but then try to return to its original route. But what happens if there is another blockage? What then? By the time the vehicle finds its way back to the route, it may well have spent more time than a human coworker would have needed to simply shift that pesky pallet.
Can’t a vehicle “cut corners” and find a new, more efficient route? Like all vehicles, AGVs need “road rules”. It may be faster for a car driver to take a shortcut (through a stop sign, or over a footpath, for example), but it’s disruptive to other road users if not downright dangerous. Similarly, if an AGV acts outside the rules and tries to plot a novel path, this could be disruptive to other vehicles and staff.
A real-world example
Let’s take a real-world example. In an article on LinkedIn, BlueBotics CEO, Nicola Tomatis wrote:
“A tire manufacturer previously operated a fleet of 37 AGVs, all of which used obstacle avoidance. When the company decided to retrofit these vehicles, however, it went with pure path-following ANT navigation in tandem with our ANT server fleet management software. The tire firm actually installed seven fewer AGVs in all. But the 30 it now uses have proven to be 10% more productive than its previous 37.”
“The 30 [AGVs] it now uses have proven to be 10% more productive than its previous 37.”
To be clear: those are the exact same automated vehicles, only transformed to run using path-following technology rather than obstacle avoidance. That one change allowed the company to operate almost 20% fewer AGVs while boosting their productivity by 10%. “When it comes to overall efficiency, that’s the path following difference,” Tomatis concluded.
Is path following the safer option?
Automated vehicles are safer than their manual counterparts. But they’re safest when they stay in their lanes (literally).
In industrial environments, vehicles that run in virtual path following mode are clearly the safer choice. They will stick to their defined routes, which can be marked physically if helpful, and staff can be trained to:
- Keep these areas clear and
- Stay out of them.
If a vehicle can roam wherever it likes, it is much harder for staff to stay out of its way. And the larger the automated vehicle, the larger the perceived risk if it starts 'doing its own thing' by navigating around blockages.
What’s the right choice for your business?
So which is the right choice of AGV navigation mode for your business - path following or obstacle avoidance?
To discuss this subject in more detail, schedule a free consultation call with one of our intralogistics experts.