Hi Julien, and thanks for taking the time to meet with us today to discuss lab automation and mobile robots. Let’s start with a quick overview of how you, JAG, see the industry today.
How are mobile robots being used today in the life sciences and pharmaceutical industries?
Today, mobile robots are really entering the laboratories, in the pharma industry, in biotech, and in the healthcare and chemical industries. We are seeing these mobile robots being used to perform inter-laboratory activities - like sample and labware transports - and for some intra-laboratory activities, where solutions like ‘mobile manipulator’ robots interface directly with formulation and analytical equipment.
At JAG we are seeing a sharp increase in the use of mobile robots in the pharma industry, for example. It's true both for the big names and for smaller-sized companies. Both of them want to achieve more with their existing teams, which means providing new tools, new workflows. The idea is to finally achieve better quality, efficiency, and traceability in the labs.
Why are companies looking to automate lab transports with mobile robots?
Traditionally in the labs, people work with SBS plates. These are filled with tubes or vials of different formats. When people are finished filling up these plates, they most commonly put them on a trolley and then they, or another colleague, transport them manually to the next step, be that another lab, quality control, temporary storage etc.
These buildings can be really big, so you can have people traveling almost the whole day with these kinds of samples. This is why we developed what we call our mobile manipulators, so that staff can focus on their own primary jobs - thinking about results, designing the next experiment - instead of having to walk to the next area.
An additional benefit of using autonomous mobile robots (AMRs) is that the transports they perform can be done outside normal working hours. This way people can have their samples or labware already in place - when they arrive in the morning, or just after lunch – which improves efficiency.
What mobile robots does JAG offer?
We have developed two different mobile robot solutions dedicated to the pharma industry.
The first is a trolley carrier or transporter AMR. This is designed to move a large range of labware, like beakers, syringes, bottles, raw materials, gloves etc. It can also be used to move used materials, for example to transport them automatically to washing machines or sterilizers, and back from there to the users.
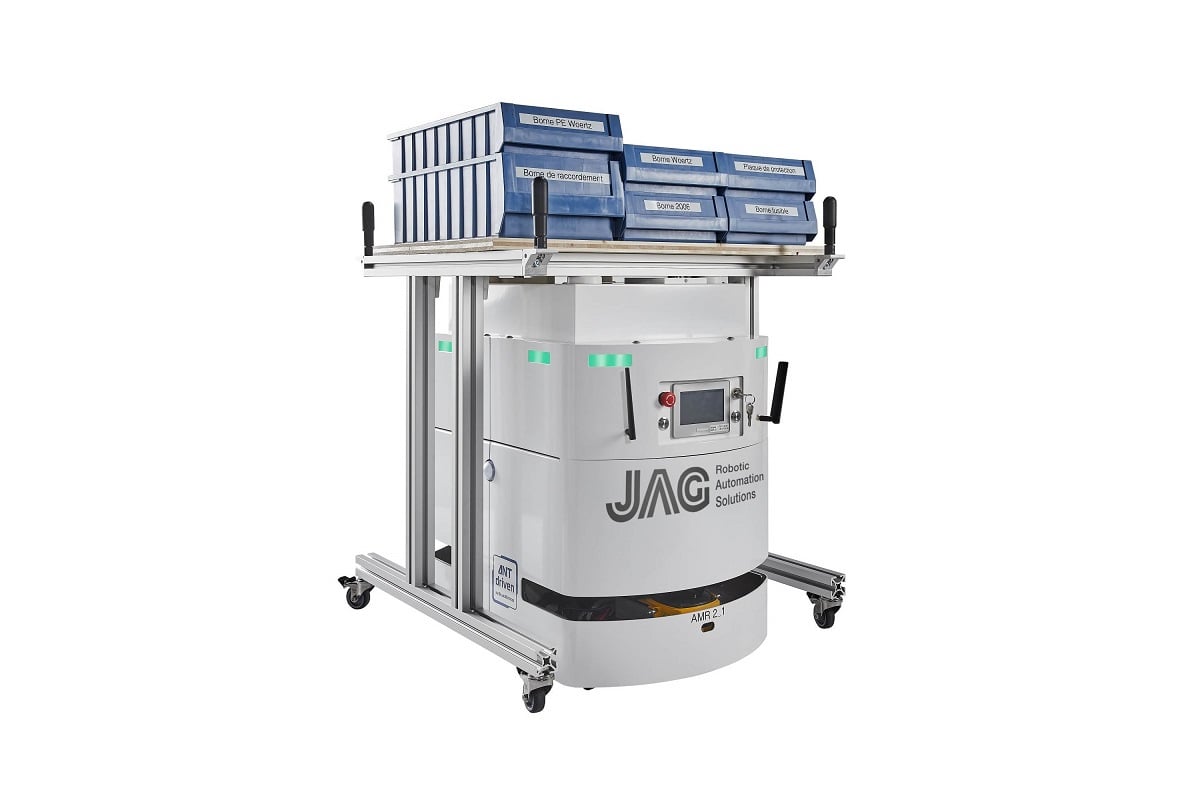
The other mobile robot we have developed is what we call a ‘mobile manipulator’ or MoMa. This is designed to move and transport materials that are held on the SBS plate format, which is super common in the pharmaceutical, biological, and chemical industries.
To go into a little more detail, the MoMa is effectively a compact autonomous mobile robot, or AMR, at its core. However, we have adapted this by adding larger batteries and onboard computers, plus we have added a dedicated closed storage system and a collaborative robotic arm equipped with a plate gripper.
The standard arm is a 4-axis model, but we also have 6-axis versions available for more complex operations and manipulations. Then we have a choice of 2D or 3D vision systems, onboard lighting, and a storage compartment capable of carrying up to 40 SBS plates, which can be refrigerated or heated for specific applications.
Although SBS is the default format, this storage system can also be customized to fit whatever format a customer prefers. For example, outside the life sciences, there are interesting use cases in the watchmaking and plastic industries, which use other plate formats that are usually two to four times bigger.
Finally, the MoMa can work alone or as part of a robotic fleet that covers different floors and building areas; it really depends on the samples and the customer’s requirements.
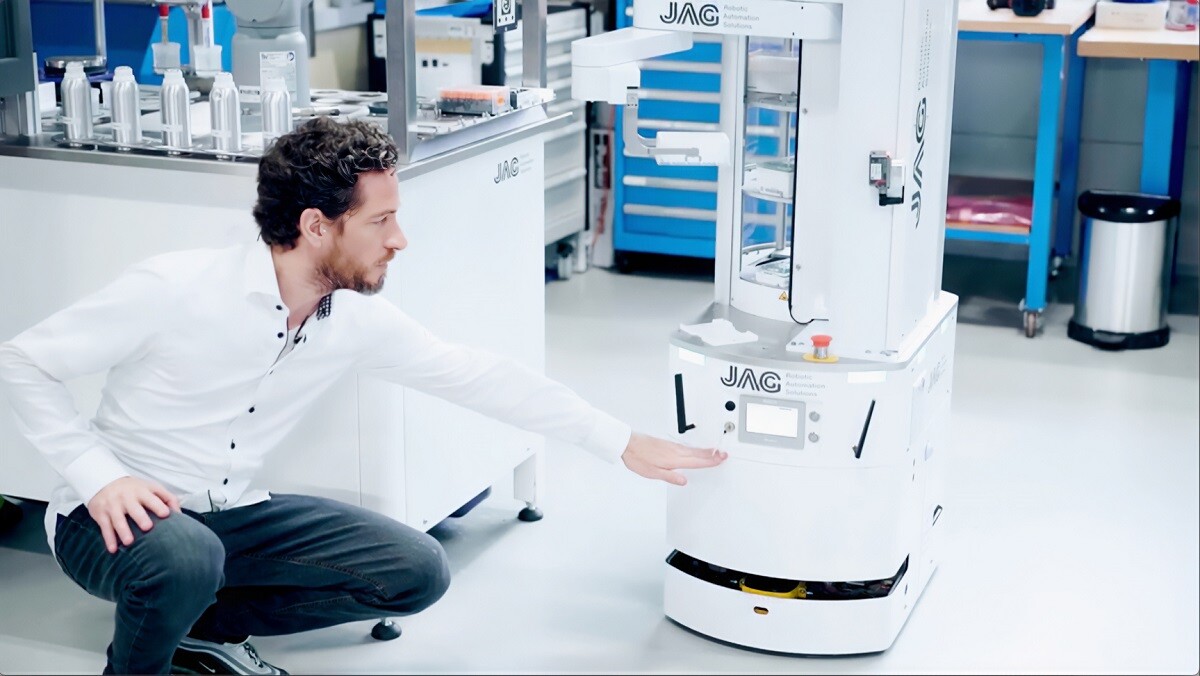
How are these robots integrated on-site and managed?
All our mobile robots are managed by BlueBotics’ ANT server, and more globally they run on the company’s ANT navigation technology.
We then connect these systems with our JAG Manufacturing Execution System. This allows us to coordinate the whole ecosystem with operators, supervisors, production machines, storage systems, and other software tools like WMS, ERP or, in the pharma industry, LIMS and operational scheduling systems.
Why did you choose to run these robots on BlueBotics technology?
We chose to partner exclusively with BlueBotics. We are using their software to map the sites where the robots will work, to plan the missions, and to manage the fleets of all of them. By working with BlueBotics, we also gain access to plenty of other AMR and AGV brands, which means that when we are working with a customer, if they have wider mobile robot requirements, there are a multitude of different ‘ANT driven’ robots available from different manufacturers, which we can choose and install as the client requires. These can then be managed via the same ANT server fleet manager project and linked from ANT server to a company’s MES for interfaces and procedures.
How do mobile robot projects work in practice?
In the pharma industry, we like to begin projects by talking a lot with customers and showing examples of what can be done, sometimes spanning different industries. The idea is to propose some ideas and to open the client’s thinking, as well as to obtain some commitment from their operational teams. This commitment is very important in order to design an efficient, comfortable and reliable robotic ecosystem.
From there, a project will grow from an initial idea to some pre-concepts, to a more detailed design stage, moving onto a real product with real functionalities that can be further upgraded afterwards. It's a very flexible process, especially in the pharma industry, which today lags behind many others in terms of robotics and automation.
Sometimes, we also run some proof of concept projects with clients. This might be required to prove a technical aspect works, like interacting with particular equipment or navigating safely and precisely in a tight environment, or as a means of obtaining more commitment, more involvement, more motivation from the client’s operational team.
What should companies know before considering automating with AMRs?
When starting a mobile robot project, especially in the pharma industry, what’s really important is to have a good leader internally; a person who will be able to talk with operational colleagues and to define with them: how they currently work, what they like and dislike, how processes can be improved, and what kind of concepts might suit their own automation project.
It is really important that a pharma company’s relationship with its robotics integrator is a long-term collaboration, not only between the integrator and a company’s internal team leader but as well with all the staff in the labs, and those working between the labs, in order to implement the right concepts and procedures so the installation performs exactly as it should.
What mistakes should companies avoid?
The main thing to keep in mind is that robotics projects are very often evolving things, especially in the pharma industry. So, it is important to keep in mind that the initial form a project takes may need to be modified as it progresses. This type of optimization really requires a constant and transparent dialogue between the robotics integrator and the client. This often takes the form of dedicated workshops, which involve not only the project managers on both sides but also the wider teams.
Can you give us any examples of current mobile robot projects?
At one customer, we have transporter robots that are travelling more than 2,000 kilometers each year. Actually, the company has three of them, so altogether that’s more than 6,000 kilometers a year.
At another customer, we have a larger robot that is running missions of up to 1.5 kilometers in length, transporting EU pallets . I mean SBS format.
And thirdly, in the pharma industry, we have a Mobile Manipulator that is transporting up to three million samples each year.
Looking ahead, what’s next in lab automation?
As well as using robots to transport labware and samples, the key players in the pharma industry are now becoming very interested in bringing mobile robots directly into production areas. This could mean the automated pouring and mixing of liquids and powders, the automated transfer of tanks – some of them really big tanks – and automating the calibration of probes and sensors. As I said, mobile robots are really now entering the labs!
Lastly, tell us more about JAG itself
Sure. JAG is a Swiss group. We have been active for more than 40 years in the fields of automation, process engineering and robotics. We have six different entities located in Switzerland, the Czech Republic and in Australia, and we work in the life sciences, chemical, cosmetics, food, automotive, electronics, and watchmaking industries.
Take the next step
To explore JAG’s lab automation robots in more detail, click here. Or to contact JAG about your laboratory’s material handling requirements, click here.