This article is part of a series on how to buy different types of automated guided vehicles and autonomous mobile robots. Already published: how to buy a tugger AGV (webinar version).
When it comes to moving full or empty pallets around a facility – for example between warehouse and production – manually operated pallet jacks and small forklifts are two well-established solutions. However, with operator recruitment increasingly a challenge and managers looking to move existing staff onto higher value tasks, simple pallet moving is an application ripe for automation. This is where pallet truck AGVs come in.
We spoke with three leading producers of pallet truck AGVs (sometimes called pallet AGVs or pallet AMRs) and asked them everything you might need to know about investing in this technology, ranging from how these vehicles handle their loads, their maintenance requirements, how best to integrate these solutions on-site, right through to the potential ROI pallet truck AGVs can achieve. We hope you find it useful.
1. USAGE AND BENEFITS
Andrés Alconchel Ibarrola (Karter): Pallet AGVs are used across a wide range of industries, including manufacturing, warehousing, automotive, pharmaceuticals, and food and beverage. These sectors often involve high-volume production and distribution, where efficient material handling is crucial. The primary appeal of AGVs in industries like these lies in their ability to automate repetitive tasks, reduce labor costs, and enhance operational reliability. Industries with continuous production needs benefit the most due to their ability to operate 24/7 and maintain high throughput with minimal disruption.
Willem Lepelaars (Nipper): The industries in which our customers operate are pharma, healthcare, plastics, electronics, automotive, FMCG, and logistics. Most often we’re dealing with the transport of raw materials and finished goods. Humans are usually actively involved in their production processes and space is often a challenge. For these kinds of applications, a compact pallet truck AGV is a great fit.
“A well-implemented AGV system results in substantial cost savings and improved productivity, validating the investment over time.”
Bernd Krebs (Stöcklin Logistik): We see pallet truck AGVs being used across all internal processes where goods need to be transported automatically, flexibly, 24/7, and cost-effectively, to and from different internal locations, either as a replacement or a supplement to manual forklift trucks. These solutions suit all kinds of industries, but our customers are mainly working in the pharmaceutical, chemical, food and beverage, retail, wholesale, consumer goods and construction industries.
Lepelaars: It’s mainly about using the AGVs to link production and logistics activities. In one direction this can mean transporting raw or packaging materials from a site’s warehouse through to a production area. But then the reverse too: transporting finished goods and waste materials from that same production area back to the warehouse.
Krebs: AGVs suit a variety of transportation processes. For example, for transport from A to B, or in circular or mixed traffic – either for the transport of pallets from the warehouse (e.g. a high-bay warehouse, rack storage, buffer lanes, etc.) to goods issue, or in the opposite direction to storage (as goods receipt). There are also transports in which, for example, goods might be transported from one floor to another using an elevator.
Alconchel Ibarrola: Primarily they’re used to automate the transportation of materials within various stages of production and distribution. Common applications we see include moving raw materials or components from storage areas to production lines and transferring finished products from manufacturing zones to warehousing or shipping areas. We’re also seeing pallet AGVs being employed in warehouses to handle inventory, for example relocating pallets between storage locations, picking stations, or loading docks.
Lepelaars: A lack of human resources is driving companies to automate their non-value added processes, in order to make human operators available for more value added work. What’s more, implementing AGVs in a production plant leads to increased safety and scalability, making them more future ready and allowing them to better control their costs.
Krebs: AGVs work autonomously, which is a clear advantage in these times of staff shortages. Their 24/7 availability makes continuous operation possible and, in turn, a significant increase in sales performance, efficiency, and optimization of a company’s material flows. In addition, employees are relieved of having to perform recurring transport tasks, making them free for other tasks, and by employing robots we see that error and accident rates are significantly reduced.
“A lack of human resources is driving companies to automate their non-value added processes, in order to make human operators available for more value added work.”
Alconchel Ibarrola: Companies are investing in pallet AGVs primarily to improve operational efficiency, reduce costs, and enhance safety. By automating their material transports, companies can reallocate their human resources to more skilled tasks, reducing manual labor and minimizing the potential for human error. This shift to automation not only speeds up their operations but also lowers their overall labor costs and reduces downtime, leading to significant cost savings. Additionally, since AGVs handle repetitive and heavy lifting tasks, this reduces the risk of worker injuries and creates a safer work environment.
Alconchel Ibarrola: They achieve this by operating continuously, without the need for breaks or shift changes, which is a limitation of manual methods. As a reliable, automated system, AGVs also minimize downtime and reduce the chance of human error, which can occur due to fatigue or inattention. Allocating human workers to more complex tasks also contributes to an overall increase in operational performance.
In our experience, companies see improvements in efficiency and productivity after implementing AGVs, even if precise numbers vary across industries. One key advantage is the mitigation of labor shortages; many firms simply struggle to find workers to perform tasks like pallet transport and AGVs are a consistent solution, allowing operations to continue uninterrupted even in the absence of manual labor.
Lepelaars: Automation adds logic to an operation. This leads directly to an increase in efficiency and productivity, as transport requests are carried out optimally. Think of just-in-time delivery, and don’t forget the ability to also reduce buffer zones, which can free up square meters of production space within a facility.
2. HOW PALLET AGVs WORK
Lepelaars: The types of payloads vary greatly depending on the industry and type of transport. Standard transport weights typically range from 250 to 750 kg. Although pallet AGVs are usually capable of transporting loads up to 1200 kg, we don’t see this often in practice.
> Search for pallet AGVs by Payload Capacity
Alconchel Ibarrola: Pallet AGVs are designed to handle standardized pallets with normal dimensions, such as European and American pallets. Depending on the model and application, AGVs can also support other types of loads like roller cages, trolleys, and carts.
The weight capacities of pallet AGVs vary a lot, with models managing loads from 500 kg up to 8,000 kg. More specialized models, such as counterbalanced or straddle AGVs, can handle even heavier loads.
Krebs: Ideally pallets in EUR format (EUR 1). However, EUR 2 or other pallet sizes are also possible. Our Japanese customers have different pallet dimensions.
Lepelaars: Pallets that provide space to drive underneath can easily be handled by a pallet AGV.
Krebs: Wooden and plastic pallets are well suited to AGV use. The pre-requisite is that they are open at the bottom, in other words they have an entry opening and can be picked up or dropped off from the floor. With our systems, pallets that are closed at the bottom can only be transported if they are raised, so that the wheel arms can reach underneath the pallet.
Alconchel Ibarrola: They are generally designed to handle standard-sized pallets such as Euro and American pallets, whether wooden or plastic. Challenges do arise, however, with non-standard or custom-sized pallets, as unusual dimensions or irregular shapes might mean adjusting the AGV or its handling system.
Lepelaars: We only offer our Nipper pallet AGVs based on ANT natural navigation. This technology allows for highly accurate navigation within a space without the need to install additional infrastructure. This means a significant reduction in installation time and minimizes disruptions to daily operations. The ANT software also enables our customers to make adjustments independently themselves, after completing our training course.
Krebs: The BlueBotics system we use works with fixed environmental features such as walls or stationary equipment. This makes it very flexible any time project extensions or changes are required.
Alconchel Ibarrola: Karter AMRs use the BlueBotics ANT navigation system, which employs the robot’s LiDAR scanners to map and navigate the environment. This system works by measuring distances with the AGV’s laser scanners and comparing these measurements to fixed features in the facility, such as walls. Combining this with odometry, the AGV can accurately determine its position relative to the map stored on-board, providing precise navigation even in complex environments.
Krebs: Our vehicles follow their specified (virtual) lanes precisely. If there is an obstacle in the way, the AGV brakes to a stop. Once the path is clear again, the vehicle restarts. This makes it clear to other road users where the vehicle is travelling and prevents them from obstructing each other. With respect to other AGVs, traffic control must be provided by a higher-level system.
Alconchel Ibarrola: At Karter, our pallet truck AMRs are designed to work alongside other traffic, including human workers, manual vehicles, and other AGVs. The vehicles’ BlueBotics navigation system and safety scanners continuously monitor the environment to detect obstacles and ensure safe operation. This constant vigilance allows the AGVs to navigate through busy environments without collisions.
The AGVs' safety systems are integrated with the BlueBotics software, enabling efficient coordination with other AGVs and manual equipment. This integration ensures that the AGVs follow safety protocols and optimize workflow, creating a collaborative and secure working space for both automated and manual operations.
Lepelaars: Pallet AGVs are designed to operate safely in confined spaces alongside people. The vehicles’ safety scanners detect objects and personnel, adjusting the driving behavior accordingly. But, in addition, clear work agreements are essential for the successful integration of a pallet AGV into the workplace.
Lepelaars: Pallet truck AGVs are designed with safety in mind, with safety guidelines and complex safety architectures ensuring a secure system. Our Nipper AGV also complies with the latest version of the ISO 3691-4 standard, for example, which includes enhanced requirements for AGV safety features and the validation of the vehicle's automated functions. This is really a standard that buyers must assess every producer against.
Krebs: With our AGV, a safety laser scanner is fitted in both directions of travel, which monitors the respective travel area against obstacles so that the AGV slows down and stops as required. If a load is picked up or dropped off, the safety laser scanner mounted under the load carrier is covered and must be deactivated for this case. For this reason, there are additional sensors in the fork tips that stop the vehicle if an obstacle is detected. There are also emergency stop buttons on the AGV, and additional safety sensors can be fitted as an option.
Alconchel Ibarrola: Pallet truck AGVs are generally safe when they are equipped with appropriate safety features and are used within a well-managed environment. Key safety features typically include collision sensors and emergency stop mechanisms. Regular maintenance is essential to ensure these safety systems function correctly, and equally, staff interacting with the AGVs should receive proper training to understand and manage these safety protocols.
In the case of our pallet truck AMRs, these are built with a strong focus on safety and adhere to ISO-3691-4 standards. Each unit is equipped with a front-facing LiDAR sensor that works in conjunction with onboard safety PLCs, which are independent of the navigation system. If a safety issue is detected, the PLCs trigger an emergency stop, with the motors configured to put as much energy as possible into stopping the vehicle quickly and safely. Additional safety options - such as blue warning lights, extra scanners, and pressure-sensitive sensors - can be added and integrated into the safety PLCs to enhance protection and adapt to specific operational needs.
3. INTEGRATION
Alconchel Ibarrola: It’s essential to start with a thorough evaluation of your facility’s layout, assessing the pathways the AGVs will navigate, including clearances and the locations of pick-up and drop-off points. We will want to ensure these routes are appropriately sized for the AGVs and their payloads, and that the floor conditions are suitable for smooth AGV operation. Careful planning of these elements will help prevent operational bottlenecks and make sure the AGVs can move efficiently throughout your facility. Additionally, we need to consider safety aspects such as establishing safety zones and providing adequate training for any workers who might interact with the AGVs. This helps to create a secure and efficient working environment, minimizing the risk of accidents and ensuring smooth operations.
Another important consideration is how the AGVs will receive and execute their tasks. An AGV needs to be programmed, or directed, to perform its functions, so it’s crucial to assess how tasks will be communicated to the AGVs, for example through any existing on-site automation systems like WMS, ERP, or SCADA/PLC that are in place. Integration between these systems and the AGVs is essential for efficient operation.
“An AGV needs to be programmed, or directed, to perform its functions, so it’s crucial to assess how tasks will be communicated to the AGVs, for example through any existing systems like WMS, ERP, or SCADA/PLC that are in place.”
Lepelaars: Implementation is about more than just purchasing hardware. It impacts workflows and it demands changes in tasks and processes. First then, choose a partner that adds value to your automation project and one that will fully support you in the process. It’s also important to understand that installing pallet truck robots requires that these are integrated with your existing software and processes to really be efficient. Pallet truck AGVs are only as smart as the tasks they are given.
Krebs: There are many points to consider. When we work with a customer we start with a full checklist, with which we ask about transport routes, space conditions, loads to be transported, environmental conditions and much more. Depending on the findings of this research stage, both the type of vehicle and the eventual number of AGVs might change.
Krebs: AGVs generally work best in a dry, indoor environment, in which: there are no major temperature fluctuations, it is not dusty, there is no risk of explosions, and ambient temperatures range from 5 to 35 °C. In terms of flooring, a facility’s surface needs to offer good grip, not deform under load, and be free of moisture, dirt and oil. Earth leakage mustn’t exceed 10 megaohms, there should be no highly reflective surfaces, and there should be no inclines or ramps above 4%.
Alconchel Ibarrola: Pallet AGVs perform best on flat, smooth, grippy surfaces. Newly coated floors that are slippery can affect an AGV’s traction and navigation. What’s more, uneven floors and significant inclines can also impact their stability. The specific degree of incline an AGV can handle varies by model, so it's important to choose a system that matches your facility.
In terms of temperature, while AGVs can operate within a standard range, extreme conditions can pose challenges. High temperatures, particularly those above 50 °C, can impact the performance and longevity of a vehicle’s electrical components. And significant temperature fluctuations, such as moving from room temperature to freezing conditions, can lead to condensation and potentially damage an AMR’s electronics.
4. SUPPORT & MAINTENANCE
Krebs: The frequency of maintenance needed changes depending on the application and whether an operation spans one, two, or three shifts per day. For single-shift operations, vehicle maintenance is usually due twice a year.
Lepelaars: Pallet truck AGVs do require regular maintenance. We typically agree a Service Level Agreement (SLA) with our clients, outlining specific terms. Broadly speaking, maintenance can range from a minimum of once per year to multiple times, depending on a customer’s expectations and usage. By usage this means not only operating hours, but also load weights, and environmental conditions such as a site’s floor quality.
Alconchel Ibarrola: Pallet AGVs require regular maintenance to ensure optimal performance and longevity. This maintenance covers checking for hydraulic leaks, securing connections, and cleaning the AGV. Key components such as the vehicle’s drive system, battery, and sensors should also be inspected regularly for wear and potential issues.
With proper care, pallet AGVs generally have a lifespan of around ten years. Batteries meanwhile last up to seven years, while drive components can last up to five, depending on usage and maintenance.
Lepelaars: Integrating AGVs into your existing workflows requires careful planning and collaboration. There are several best practices that we follow.
We start by assessing a client’s current processes – analyzing their existing workflows to identify areas where AGVs can add the most value, such as repetitive tasks or heavy lifting. We involve stakeholders early – engaging key departments and employees from the start to minimize their resistance and ensure that the system aligns with the business’s real needs. We run pilot testing in a controlled environment to fine-tune the integration and address any operational challenges. We also provide comprehensive training for employees on how to interact with the AGVs and adjust their tasks accordingly.
I would add that what companies are realizing more and more now is the importance of choosing a technology partner who understands your business goals and can offer both technical expertise and long-term support. And, last but not least, after deployment we continuously monitor the performance of a customer’s AGVs to make any adjustments to workflows or system configurations necessary to further maximize efficiency.
Alconchel Ibarrola: It involves several key steps. Firstly, we start by evaluating your current operations and workflows to identify areas where AGVs can provide the most benefit. This includes mapping your facility’s layout, including pathways and key pick-up and drop-off locations, the aim being to assess how AGVs will fit into your processes and where they can streamline operations.
Next, we need to address system integration. AGVs need to receive their tasks automatically, which involves linking them with existing systems like WMS, ERP, or SCADA.
The typical architecture flow sees the WMS/SCADA system send a request to the BlueBotics ANT server fleet manager, which in turns sends an AGV mission to the AGV. Effectively, ANT server acts as a communication hub between the WMS and the AGV fleet, translating operational needs into AGV missions. ANT server can assign tasks to AGVs based on real-time WMS orders. It also coordinates communications between the AGVs and other facility infrastructure, such as automatic doors and elevators; when an AGV arrives at a door or elevator, it informs ANT server, which then triggers the necessary action (e.g., opening the door). This coordinated interaction ensures AGVs work fluidly within a client’s existing facility.
Finally, it’s important to train your staff on this new technology and maintain clear, unobstructed paths for the AGVs to move along. And make time to regularly review the system’s performance, adjusting as needed to ensure it keeps running efficiently.
Krebs: On the customer side, it’s important to involve employees in the automation process at an early stage and show them the benefits and advantages of AGV systems. Otherwise, there may be disagreements later on. Also important are a thorough analysis of your existing processes and good consultation and agreement with your integrator.
Once all the technical details of your future automated processes have been clarified, the routes of the AGVs can be planned in advance. This significantly reduces the time needed for commissioning on-site, and the transitions between manual and automated transports can be relatively smooth.
Often, what we see at Stöcklin is that, at first, only a part of the process is automated, but after working with the system the customer realizes the benefits and then decides to automate further parts of the process, with our support.
Lepelaars: We train all users of our Nipper system in full. The goal is to transfer our knowledge to the customer’s team so they can establish internal ownership of the project. In addition to providing expert training to so-called Super Users, we also conduct on-site operator trainings. This ensures that the people who will encounter AGVs in their daily work understand how to interact with them properly.
Krebs: After each AGV commissioning, the customer receives instruction on how to operate the vehicle and the system itself. In the event of malfunctions, we offer the customer remote support and, of course, we also provide their personnel with detailed product training.
Alconchel Ibarrola: At Karter, we start by providing extensive training to our integrator partners on the hardware and software of our AMRs, including installation and commissioning. Our integrators also undergo specialized BlueBotics training to gain a deeper understanding of the vehicles’ navigation software, which ensures our partners are well-prepared to handle AMR projects and to offer technical support to end customers.
After receiving this training, our integrators pass their knowledge on to a facility’s personnel, focusing on both the operation and maintenance of the AMRs. This training includes guidance on basic troubleshooting and maintenance to help a customer’s team manage the systems effectively and, as much as possible, to be able to address minor issues independently.
5. INVESTING IN PALLET AGVs
Lepelaars: A key single consideration is total cost of ownership. With this in mind, factor in not just a vehicle’s initial purchase cost, but also its associated long-term costs, including maintenance, energy usage, and potential downtime. Most importantly, find a partner to work with, not merely a supplier.
Krebs: The three main considerations I would advise are: How quickly will such a system pay for itself (ROI)? Does the system offer the flexibility you need in terms of your flow of goods and the transports needed in a required time. And lastly, how easy will it be to implement the AGV within your current system?
> Explore our AGV ROI Calculator
Alconchel Ibarrola: Begin by evaluating how the AGV will fit into your existing processes and facility layout. Assess the AGV’s compatibility with your current operations, including the maximum weight and volume of your different loads, the distances the AGV will have to travel, and the number of pick-up and drop-off points. From there we can determine the number of AGVs needed, based on your workflow requirements and how these vehicles will integrate with your current automation systems.
“Factor in not just an AGV’s initial purchase cost, but also its long-term costs, including maintenance, energy usage, and potential downtime.”
It’s also crucial to understand if your Warehouse Management System (WMS) or control systems can automatically send missions to the AGVs, or if adjustments are needed to accommodate this process. Additionally, consider your specific safety requirements to ensure the AGVs in question can meet these.
After evaluating these integration factors, you can then compare the technical specifications of different AGVs, such as their load capacity, speed, battery life, and charging needs, to ensure they align with your operational demands. Then review the environmental conditions of your facility, including flooring, inclination, and temperature, as these factors can affect the AGV's performance. Understanding how the AGV will interact with your current processes and staff is also important to optimize your workflows.
Finally, consider the total cost of ownership, including required maintenance and potential downtime, to assess the overall return on investment and ensure that the AGV system will provide real value over its lifecycle.
Alconchel Ibarrola: The return on investment of an AMR depends on several factors, including the scale of automation, the ease of integration with existing systems, and the volume and frequency of material handling. Facilities that operate around the clock and manage a high throughput of material generally experience a faster ROI, as AGVs significantly reduce the need for manual labor and improve workflow efficiency over multiple shifts.
Customers running single eight-hour shifts usually see a payback period of approximately one to two years. This period can be shorter though for facilities operating 24/7 or with more frequent shifts, as continuous AGV operation maximizes savings and throughput. Of course, the exact figures can vary, but our experience indicates that a well-implemented AGV system often results in substantial cost savings and improved productivity, validating the investment over time.
Lepelaars: The number of shifts (working hours) per day is the biggest driver in achieving ROI. Typically, we can say that ROI is usually achieved within one to three years.
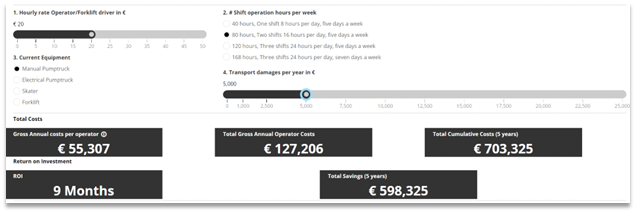
Krebs: It is always very individual, so only the customer can really confirm that as only they know what their labor costs are, and therefore how quickly the system will pay for itself. One of our customers informed us, however, that their AGV had already paid for itself after nine months of operation.
Ready to talk pallet truck AGVs?
Are you interested in automating your business' pallet moving processes? If so, click here to browse ANT driven pallet AGVs, or contact our expert team to book a free consultation.