.png?width=1920&height=1258&name=Automated%20vehicle%20workflow%20in%20FMCG%20warehouse%20(1).png)
To move potatoes to dining tables throughout Poland, Awex has a custom-built distribution center – and the usual issues that come with it.
“The key issue was that the conveyors Awex was using were frequently damaged as pallets were picked and dropped between the conveyors and banding machine with manual forklifts. And due to the small space, there were collisions between the forklifts too,” explains Łukasz Awsiukiewicz, Co-Founder and System Engineer at Nipper Polska, the integrators behind the installation.
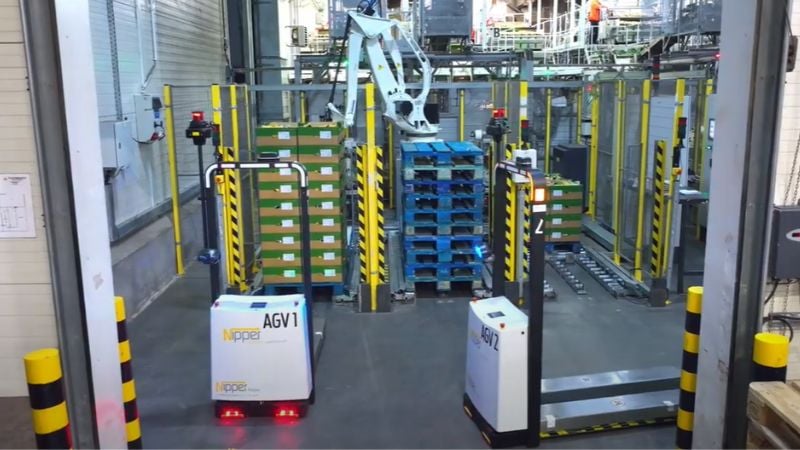
While occasional mistakes are an inevitable cost of doing business with human workers, the Awex team was facing an additional challenge: “Awex planned to increase the speed of the lines, and the total number of pallets processed per hour.”
As these changes weren’t possible simply by increasing staff numbers, and with the damage issue on top of that, the decision was made to automate the movement of pallets of veggies between the conveyors and banding machine.
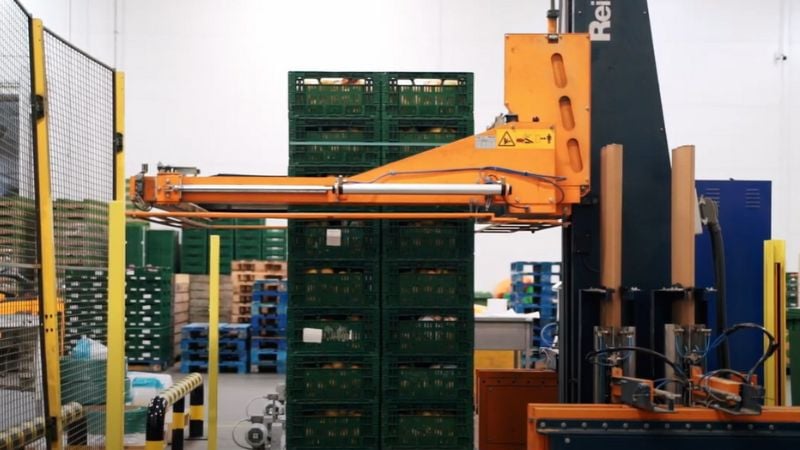
Awex's team first considered installing a further series of conveyors, but decided in favor of AGVs due to the additional flexibility these mobile robots offer: should the business’s needs change in future, the vehicles can be reprogrammed quickly and easily. "It is easier to reprogram an autonomous vehicle than to rebuild the entire conveyor system," says Łukasz.
> See also: AGV/AMR vs Conveyor – Which is the Right Choice for Your Business?
Value-added: Automation without stopping production
FMCGs have to keep moving: the facility was automated without stopping production. Łukasz says: “What was important for the company was a solution which could be implemented without stopping the entire production line.”
The Nipper could work in parallel to the existing manual forklifts while acceptance testing was carried out. Plus, the vehicle's low profile was an asset: it was important to the team that the vehicle could pick up and drop off pallets directly from floor level, so that additional racking did not need to be installed, which would have inevitably disrupted work.
“We performed site acceptance testing with the Nipper AGVs in February 2022. The solution was then deployed in two phases,” says Łukasz. “First, we did a test run with one AGV. Then after validating all nodes [in ANT lab software] we ran a pre-site acceptance test to check if the AGVs kept their accuracy on the map. And then we were ready to go!”
Details: Automation of fast-moving consumer goods distribution
Project details | Forked AGVs in an FMCG distribution center |
---|---|
Location | Kościuszków, Poland |
Vehicles | 3x Nipper AGVs |
Integrator | Nipper Polska |
Customer | Awex |
Software | ANT lab (configuration software) ANT server (mission and fleet management) Custom web-based HMI developed using Node-Red |
Automating a FMCG workflow
Before introducing forked AGVs, the Awex team looked carefully at the existing workflow. As well as reducing the number of collisions to zero, integrating the strapping machines with the vehicles improved efficiency.
.png?width=1920&height=1258&name=Automated%20vehicle%20workflow%20in%20FMCG%20warehouse%20(1).png)
Broadly, the workflow was simply moving from A to B and back again. Pallets full of veggies were picked up from either conveyor belts or the co-packing area, depending on the days work, and moved to the strapping machine. The load is wrapped according to type, and then moved to the shipping area by conveyor. Empty pallets are returned, and the cycle starts again. Watch the video to see this workflow in action:
Finally, to improve the process still further, the strapping machines were configured to work based on load, switching between different strapping types for paper cartons and plastic boxes. This means that as well as shifting goods, the AGVs communicate with the equipment. As we discuss below, this was achieved with an on-site PLC.
Today, the vehicles run two eight-hour shifts between 6 am and 10 pm, moving around 300 pallets a day. As they work in parallel to their human counterparts, the AGVs take three breaks during operating hours – the perfect moment to recharge their batteries. Battery charging takes just 30 minutes, so in practice, the AGVs are always available.
And all of these tasks take place in a tight space: “The three vehicles had to work within an area of around 60 meters square,” says Łukasz. “Luckily the Nipper is very agile and compact, which makes it ideal for small spaces.”
“For us the most important fact was that Nipper AGV, with its BlueBotics navigation system, offers is very repeatable and accurate movements,” he adds.
Communicating via PLCs
Packaging requirements change depending on whether the veggies are packed in plastic tubs or cardboard boxes. By communicating via the project’s ANT server fleet manager, the banding machine’s PLC can learn when any given carton was taken from which line, and therefore what load it contains and whether extra carton reinforcement is required before the straps are applied.
“The vehicles interact with two PLCs to confirm that the magazine was loaded with a full pallet stack. It also communicates with the banding machine to change presets to match the load,” says Łukasz.
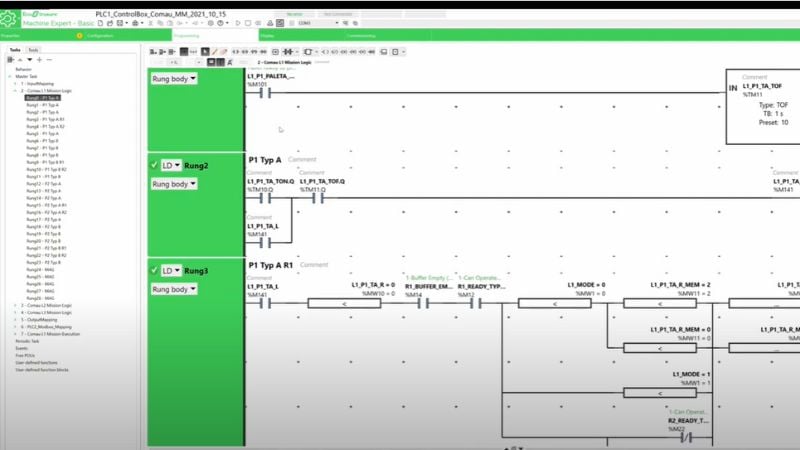
The vehicles are programmed using ANT lab software, and complete the vast majority of their tasks without instructions from human co-workers. However, a custom web-based HMI (human-machine interface) was also developed by the Nipper Polska team using Node-Red to allow the AWEX team to speak directly to the Nippers as needed. This HMI can be accessed from screens placed strategically throughout the facility. Using it, operators can check on the status of the vehicles and their current missions. They can also call new missions as required. Watch the video to see this in action:
If there are any issues with the vehicles, the team can run diagnostics and resolve the issue from within the HMI.
Human operators are also charged with keeping the AGVs’ safety laser scanners clean, since fresh-picked veggies emit plenty of dust.
Success without affecting staffing numbers
The team estimates that the vehicles have already travelled over 2,500 kilometers within their operating area of just 60 square meters. That’s a lot of vegetables moved.
AWEX’s AGV project has been so successful that its team plans to expand its use of automated vehicles. Łukasz comments that, “This current Nipper project is just the first phase. The next step will be to transport pallets to a holding area, and then from the holding area to a picking area.”
And this success came without losing team members. AWEX’s manual forklift drivers have been reassigned to different duties, other jobs were created through the automation process, and the overall number of staff remains the same. “There is also now a dedicated forklift and AGV coordination engineer in place for doing more advanced jobs and being the first service contact,” adds Łukasz.
“The automation project helped reorganize the operation area and allowed the team to install a higher efficiency line – all while maintaining the same crew size,” Łukasz concludes.