Every year, around 180,000 trucks of all kinds – from firetrucks to semitrucks – roll out of Sinotruk’s Laiwu factory. One of the final steps in the manufacturing process is inspecting the paint of a truck’s cab before it hits the road.
While not much thicker than a human hair, automotive paint can dramatically cut down on maintenance and make a material difference to the lifespan of a vehicle. That’s why controlling for the correct application of paint is a crucial step before the truck cab leaves the facility.
The paint job of every truck cab is carefully checked, although only a small percentage of vehicles needs extra attention. EcoProFleet paint shop AGVs by Dürr move cabs in and out of spot repair boxes as needed, ensuring every vehicle has a robust coat of paint before leaving the facility.
Project details: Paint shop robots
Company | Sinotruk |
---|---|
Location | Laiwu, Shangdong Province, China |
Robots | 2x EcoProFleet AGVs by Dürr |
Control software | Dürr DXQlogistics.control |
"Breaking the line": automation in automotive production
The line production has been the gold standard of automotive manufacturing for over a century. But while efficient, lines are also prone to bottlenecks: one interruption at any point in the line can cause a cascading series of delays. The facility’s Dürr AGVs allow the Laiwu team to “break the line”, moving truck cabs in and out of the line without causing bottlenecks.
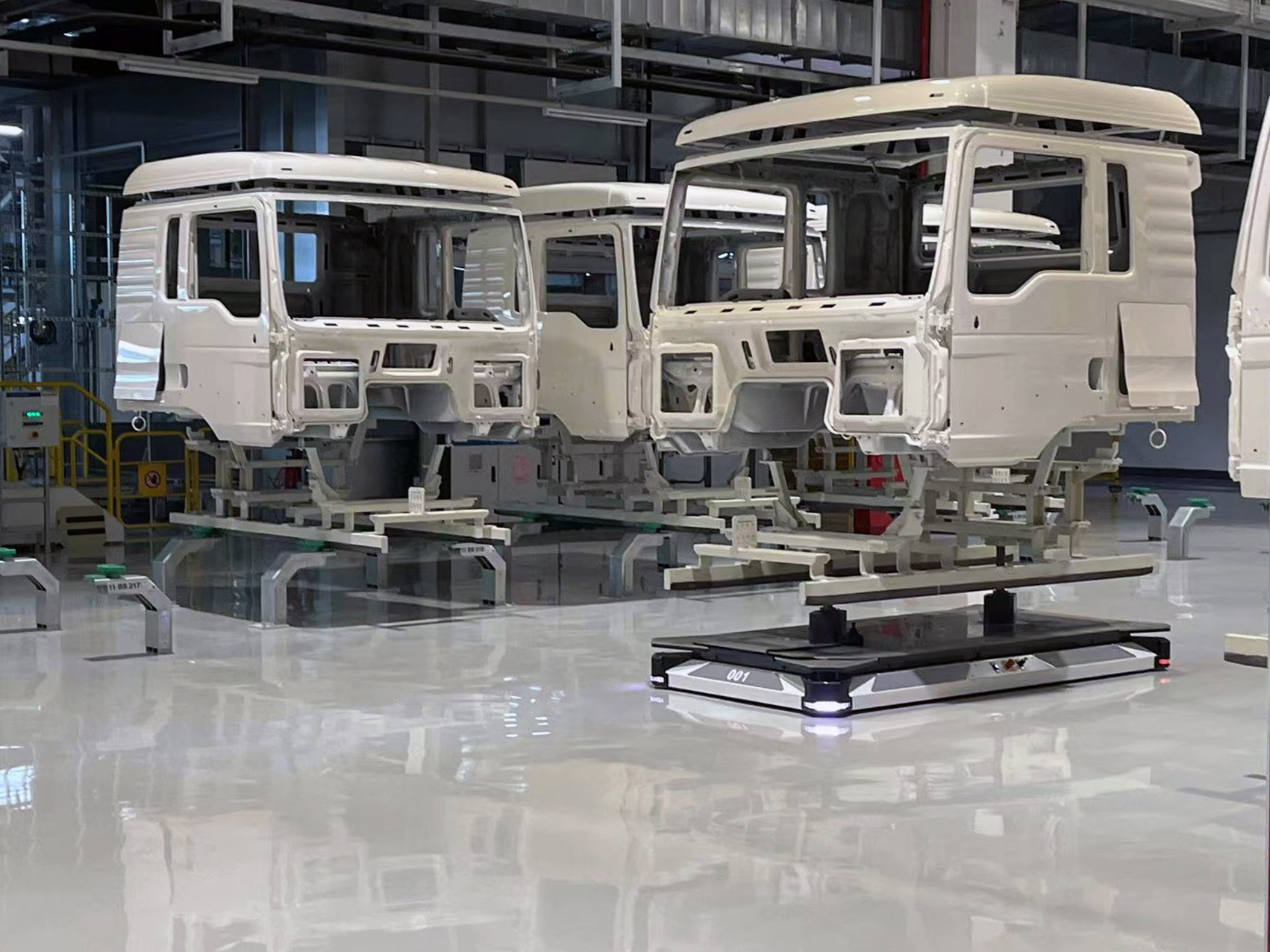
“We look at matrix production versus line production,” explains Stefano Bell, product manager at Dürr Systems. When examining how many vehicles could be produced in total, rather than at what speed they roll off the production line, “AGVs allow a lot more flexibility.”
This flexible approach is aligned with “no fault forward” manufacturing strategy. Production is checked at every step, and anything that needs extra attention is dealt with before moving to the next stage of manufacturing. In the case of Sinotruck, almost-complete truck cabs roll along a conveyor and are manually inspected. If a worker sees that part of a paint job needs attention, they simply press a button next to their station. This summons an EcoProFleet AGV to remove the cab from the line and shift it to a parking area, without interrupting the overall production flow.
%20How%20the%20paint%20shop%20robots%20by%20Durr%20work-png.jpeg)
The importance of auto paint
Automated guided vehicles have been used in automotive manufacturing for decades. But as Bell explains, “Trucks are totally different from cars.” Compared to cars, which tend to be reinforced to protect their passengers in case of collision, “Truck cabs are stripped down, with fragile metal on top.” That means paint is even more important: as well as being an aesthetic choice, paint actually helps protect the vehicle.Paint acts as a seal, stopping moisture from reaching the truck’s body, preventing rust and dramatically extending the life of a vehicle. Sunlight, road salt, acid rain, mud and dust, and even bird droppings can break down paint – not to mention chips from stones and scrapes or other damage.
That’s why it’s essential that paint is checked and extra attention given as needed. A perfect paint job reduces the need for maintenance long-term and extends the life of the vehicle.
Throughout the manufacturing process, the cab of each truck is mounted on specially-designed skids which remain attached. While the base of each truck cab has a slightly different design, the skids are standardized and can slot neatly into the EcoProFleet AGVs and other equipment in the facility.
This means that when the Laiwu facility pivots to creating different vehicles, the lines will not need to be reworked.
The process is managed with Dürr’s DXQlogistics.control software, which offers end-to-end tracking of parts, chassis and skids. At any point, the Laiwu team can monitor the flow of material, and even control the AGV fleet from within the software, which is in turn linked to the company’s site-wide Manufacturing Execution System (MES).
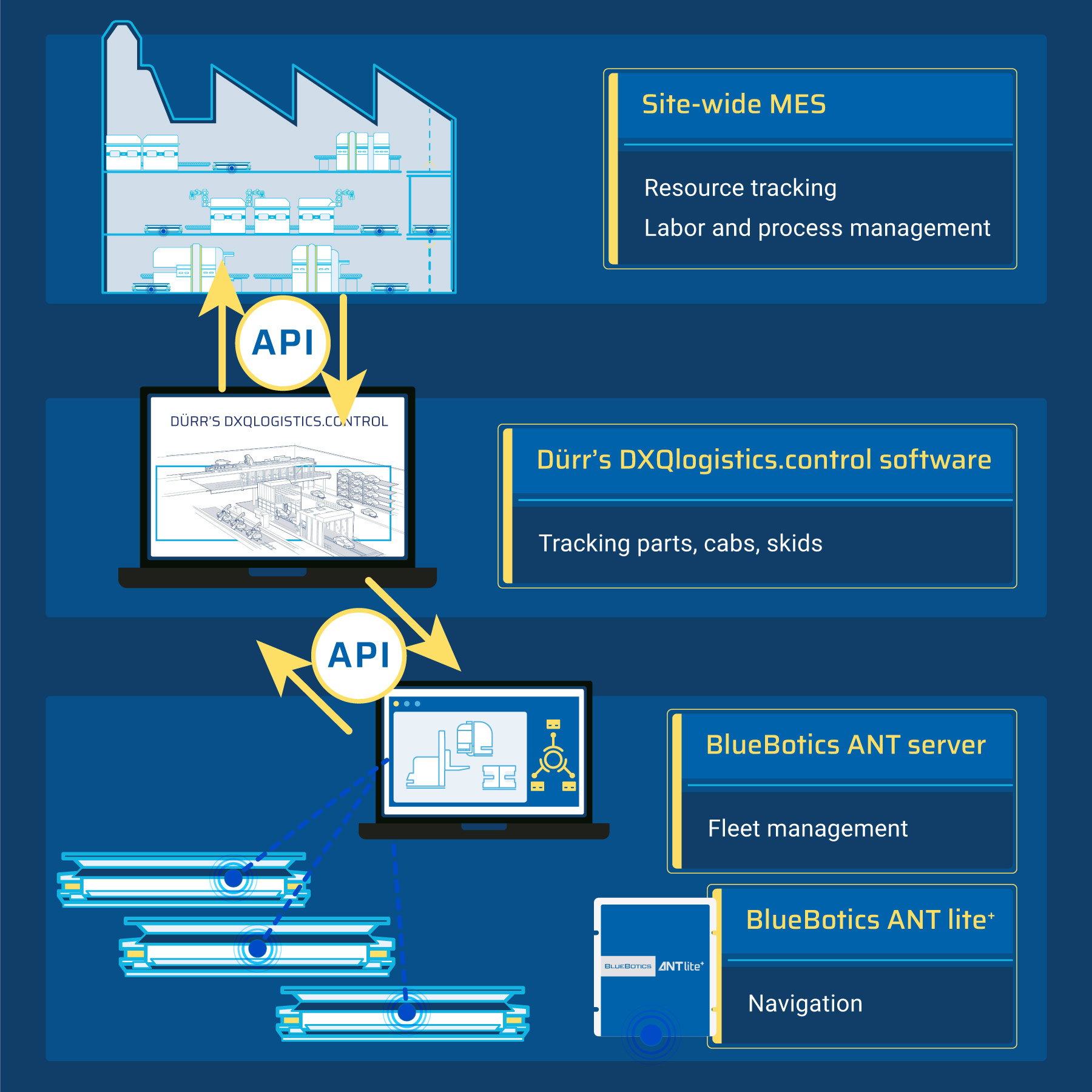
The individual EcoProFleet paint shop AGVs by Dürr are controlled by the built-in ANT navigation technology by BlueBotics. This allows them to “know where they are” and accurately navigate through the environment.
Together, the small fleet of AGVs is controlled by ANT server. This software automatically controls traffic, and manages vehicle charging.
ANT server communicates with Dürr’s DXQlogistics.control software via API, which tracks material throughout the facility. In turn DXQlogistics.control communicates with the site-wide MES.
It seems complex, but from the point of view of the workers on the floor, the EcoProFleet AGVs “just work” – transporting cabs from line, to parking bay, to spot repair box and back again as needed.
Charging stations
A truck cab and the skids it is mounted on weighs around 850 kgs (around 1,850 pounds), meaning it takes a tremendous amount of power to move.
However, “The AGVs do not use batteries – they use capacitors, supercaps” says Bell.
“The charging spot is on the transfer station, and the AGV always returns there after moving a load, so whenever it stands still, it’s charging.”
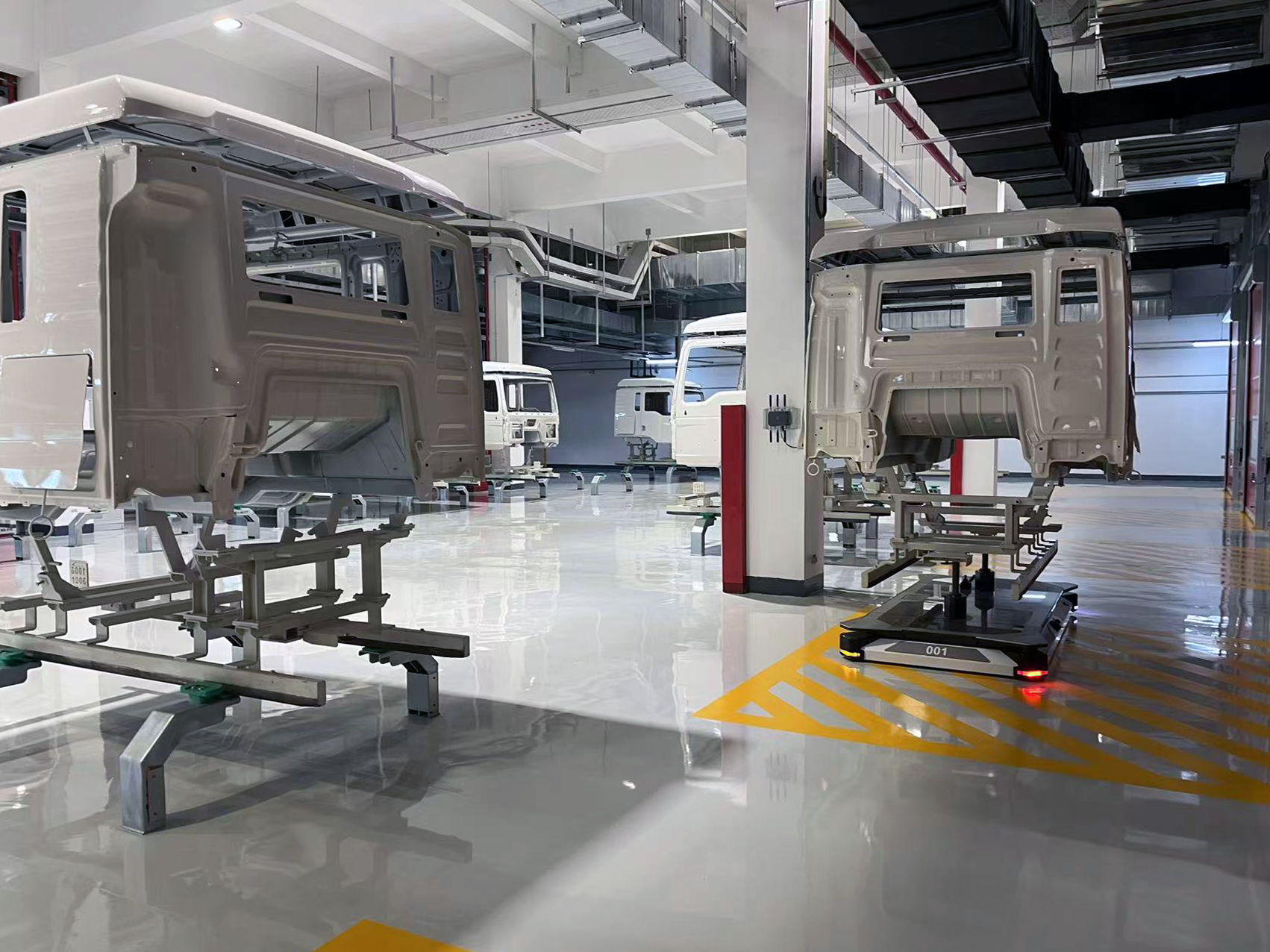
The supercapacitor will only power a fully loaded AGV for around ten minutes, but this is ample time for the project’s needs – and reaching a full charge only takes two minutes.
And they don’t stop: the EcoProFleet AGVs work 24 hours a day. The fleet moves at a leisurely 60 meters per minute (slowing further to 15 meters per minute around workers).
Power up: Batteries, Capacitors and Supercapacitors
What’s the difference between a battery and a capacitor? What about the difference between a capacitor and a supercapacitor?Batteries, capacitors and supercapacitors all store and then release charge: the difference is in the details.
- Batteries use chemical energy: they store and then release power using chemical reactions.
- Capacitors use kinetic energy: they convert the kinetic energy of charged particles into electrical energy. They can store – and then discharge – power much more rapidly than a battery.
- Supercapacitors are sometimes called double-layer capacitors. They work in a similar way to capacitors, but have a layer of activated carbon which allows them to act something like a battery as well as like a capacitor: they can store and release both chemical and kinetic energy.
Flexible and future-proof
“If you are only producing one sort of vehicle with a high throughput, you may not need a flexible conveying system,” says Bell. “But different vehicles have different requirements... for example, if you’re making an SUV and a sedan in the same production facility, you may have different processes, and an AGV can give you that flexibility.” Plus, “AGVs allow smaller buildings as you can use mixed spaces [as automated vehicles can work alongside humans].”
The greenfield site at Laiwu is such a success that another is being built around two hours away, at Zhangqiu. “The feedback from colleagues is very good – the AGVs are very reliable,” says Bell.