Optimizing before automating
Steven Lockhart had a challenge: increase efficiency while optimizing human resource costs.
As the head of GECOM Corporation’s Continuous Improvement team, Lockhart had seen automated guided vehicles (AGVs) in action at other GECOM sites. In 2018, he decided to look more closely at this approach by embarking on an AGV adoption program at his company's auto parts production site in Greensburg, Indiana.
“We had material handlers with pallet jacks walking around trying to figure out what they needed, when they needed it,” Lockhart says. So, with clear room for improvement, and a headcount reduction target to meet, the team decided to move, step-by-step towards automation of its material handling processes.
The steps Lockhart and his team followed were:
- Optimize existing processes and find efficiencies using manual vehicles
- Introduce a few AGVs/AMRs as a proof of concept
- Move forwards with a full automation program
The project proved worthwhile from the very first step.
“We never had a good time study to tell us if we had the right number of people or not.”
The Continuous Improvement team surveyed the shop floor. Material handling associates were moving empty tubs (boxes) and raw materials from the warehouse to one of the plant’s 65 assembly lines and then returning full tubs of finished products. This manual process meant high pedestrian and lift truck traffic on the floor – which was at odds with GECOM’s safety-first policy.
“We never had a good time study to tell us if we had the right number of people or not. So, we knew we had some good opportunities to optimize our processes,” concludes Lockhart.
Before introducing automated vehicles, however, the team first employed manually-driven tuggers (tow tractors) pulling carts full of tubs.
“Our thought was that we could implement the tuggers and then transition from the tuggers to AGVs. Implementing the tuggers first would allow us to establish the routes and the pick and drop points, which would be one less challenge once we started with the AGVs,” Lockhart explains.
The tuggers allowed the material handling associates to move five skids at once. Working more efficiently, they moved components from the warehouse to the assembly lines, shifted skids of empty tubs to the lines to collect the finished goods, and finally returned full skids of finished goods from the assembly lines to the warehouse.
“We were already able to achieve some headcount optimization by running one tugger, pulling five carts at a time,” says Lockhart.
With potential savings already identified, the team moved forwards to the second step: finding and introducing the right automated guided vehicle.
Automation with warehouse AGVs
Customer |
GECOM Corporation Automotive |
---|---|
Industry | Automotive |
Location |
Indiana (USA) |
Employees | 630 |
Forked AGVs | 5x "Nipper" forked AGVs by Nipper |
Control software | BlueBotics ANT server Ignition SCADA software by Inductive Automation |
Expected ROI | 2 years |
Choosing a forked AGV for a tight space
Like many manufacturers, the GECOM team had limited space in which to work.
“Our assembly floor is pretty tight; there’s just not a lot of free room,” Lockhart says. “In theory, the tugger driver could have done it, but we knew that wouldn’t be possible if we were using AGVs and we were trying to eliminate all human interaction. For these reasons, we concluded that using larger AGVs such as tuggers wasn’t going to be feasible.”
Further limiting the team's choice of vehicle was the skids being transported.
“Our carts are 18 inches off the ground. Then, from the bottom of the skid to the top layer of tubs, that’s another 50 inches, a total of 68 inches high,” Lockhart says. “That meant the top tub was physically too high for our associates to stack.”
Since the top tub in a stack couldn’t be manually unloaded without an associate clambering up a ladder (again, at odds with GECOM’s safety-first policy), the team knew that a tow tractor system wouldn’t be fit for purpose – whether it was manual or automated.
“I was immediately able to narrow down a lot of AGVs because our aisles are only 96 inches [244 cm] wide,” Lockhart says. “That proved to be the biggest challenge—finding an AGV that can operate in an eight-foot aisle.”
“As soon as I saw the Nipper, I thought, ‘That’s it!’”
Working with a third-party AGV integrator, the GECOM team ran several demos of a well-known brand of autonomous mobile robot (AMR). With hooks on the back of the vehicle, these smaller units could potentially be operated like the manual tuggers the team had been testing.
But the AMRs still required manual work by associates and failed GECOM’s stringent safety policy.
“When we analyzed the safety of those robots, backing up with no safety scanner at the back, and we saw the amount of time needed to hook and unhook the AGV to the carts, we decided to look elsewhere,” he recalls. “As soon as I saw the Nipper though, I thought, ‘That’s it!’”
“Ever since I started talking with Nipper, their support has been phenomenal,” says Lockhart. “They’ve always come back with answers to my questions and they’ve always been very responsive.”
Partial automation: The first warehouse AGVs hit the shop floor
Having identified their preferred solution, the team moved to the second step in its staged process: introducing a couple of vehicles as a proof of concept.
Lockhart and his team purchased two Nipper pallet trucks, a type of forked AGV.
What’s in a name? Forked AGVs vs. automated forklifts
Forked AGVs (automated guided vehicles) and automated forklifts sound similar, but they describe different vehicles.
- Automated forklifts are manual forklifts that have been redeveloped to work autonomously. As a result, these vehicles often offer hybrid operation, enabling them to operate alone or be driven manually should this be required.
- Forked AGVs however have been built from the ground up to be automated vehicles. As they are not designed for human use, they are often smaller than automated forklifts, which often still include seats and steering wheels. For this reason, they do not offer hybrid operation.
“With two Nippers I could work out how many we’d need in total to achieve our optimization goals, by calculating our timings, routes and everything. Plus, we could verify how they interacted with each other, at intersections for example and in the systems’ software,” Lockhart says.
Before the vehicles arrived on site, the team figured out how exactly the vehicle would run, working with Nipper’s team to run simulations ahead of time.
“One of the things that really helped was using the Nipper’s ANT lab software to run a simulation before we had the AGVs on-site. So, we did a lot of work before the vehicles showed up. We had our spots on the floor, our pick and drop points, all done,” says Lockhart.
While both ANT lab and the vehicles’ ANT server fleet management software worked well “out of the box”, the team took advantage of the latter software’s API to add an additional, more expansive interface on top in order to make life easier for its team leaders.
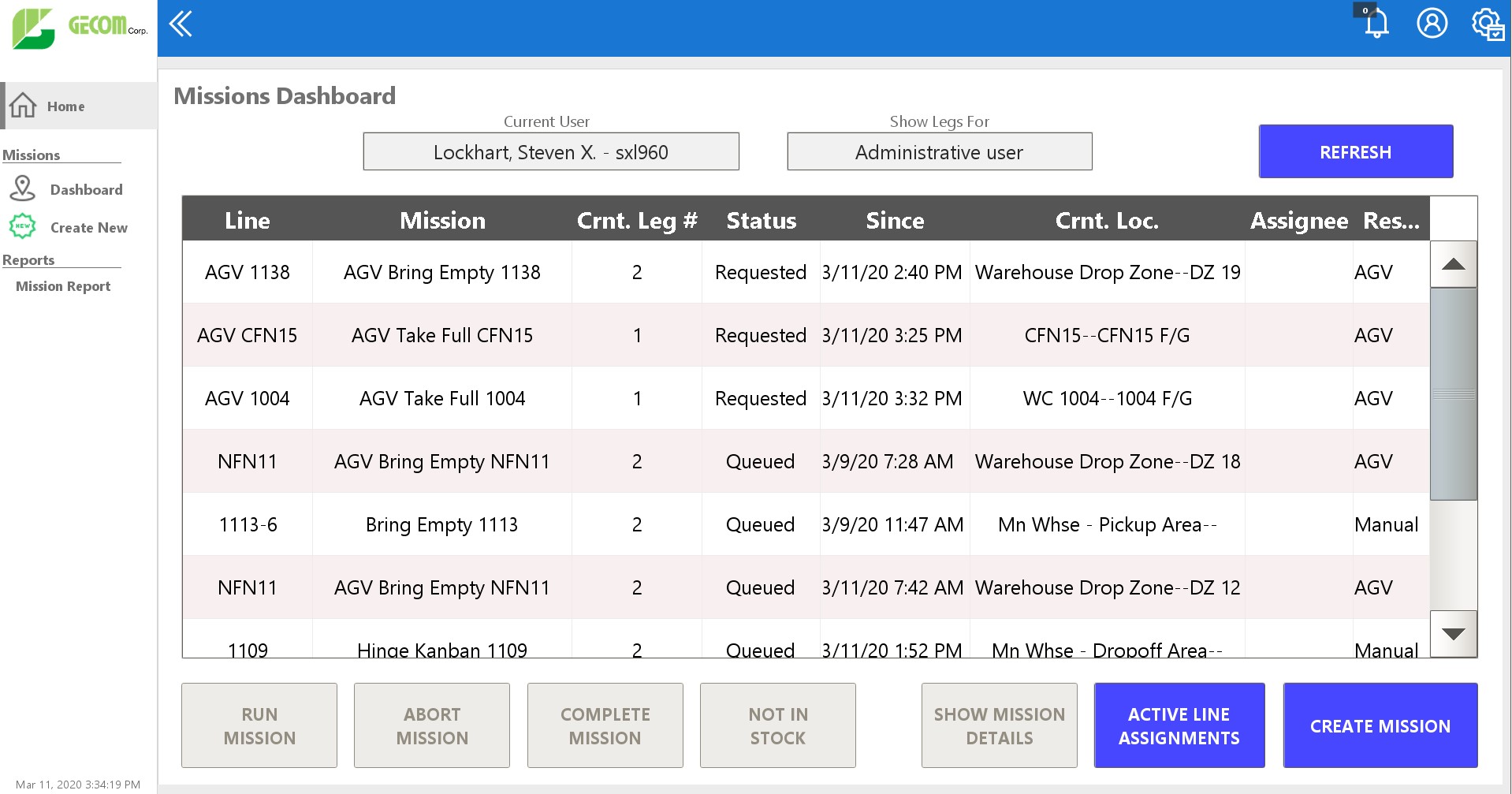
Before the AGVs arrived, GECOM's associates used the same intuitive interface by Inductive Automation to run missions as stand-ins for the AGVs. Later, this same software was linked to the Nipper’s ANT server software by API.
Ignition by Inductive Automation, a SCADA program, was connected to ANT server’s API and run on the team leader’s new tablets. This software allowed the team leaders to call AGV missions and to see at a glance which tubs need to be moved and when the finished goods were coming off the lines.
“We implemented tablets for team leaders, instead of their desktop computers, partly to make them more mobile,” says Lockhart. “We can also use the tablets to do other things on the line that team leaders need to do, like running lot control — scanning parts when these come into the line — so we know what batch of parts was used on what day. There are different things like that, which help the team leaders become more efficient.”
This customized approach helped the team “work smarter” Lockhart explains: “I could set up a team leader to only have access to their lines, which saved them from having to scroll through a long list of lines every time they needed to call a mission. Our end goal was that when he or she hits Start Mission, that mission would go into the ANT server and generate the mission for the AGV.”
When the AGVs arrived, Lockhart adds, We were able to slide the material handler tablet out and slide the AGV in place. We weren’t trying to put in two new pieces at once.”
Installation and automation
With its processes nicely ironed out, the team was ready to bring in its warehouse AGVs.
Commissioning (installing) the first two Nippers in April 2019 took around two weeks. Nippers three and four were then installed in September 2019, followed by Nipper five in March 2020.
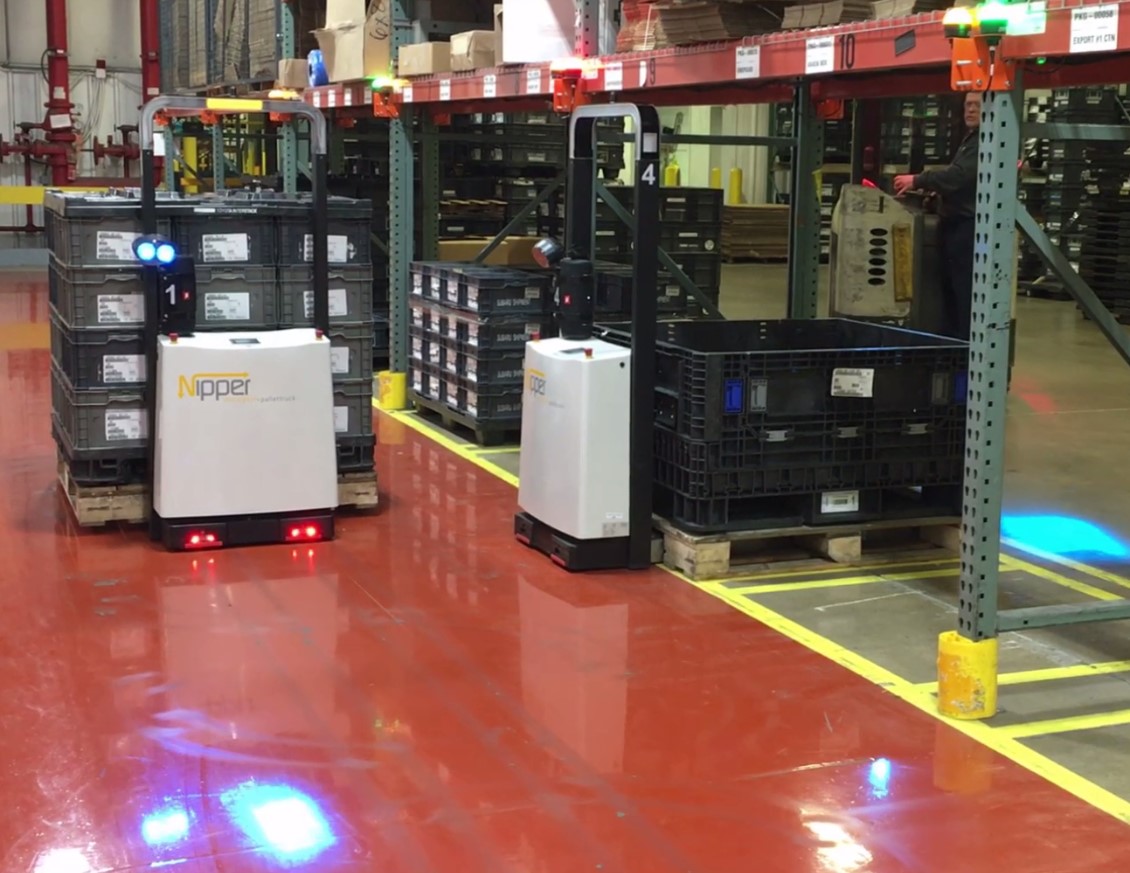
Installing the subsequent AGVs was a fast process. “With AGVs three to five, we knew what we wanted to set up beforehand and we were able to make all of our lines for the AGVs to interact with the API. So, we did a lot of that set-up before AGVs three to five got here,” says Lockhart.
Lockhart’s biggest installation challenge? Human staff getting used to the machines. “No one has had AGVs here before, not associates or team leaders. So, one thing was just getting them accustomed to these vehicles, getting them to understand how they work. For example, everybody kept walking through the fields of the Nippers’ safety scanners, so we had to carefully explain how these scanners worked so that this didn’t happen,” Lockhart says.
Automation ROI: Breakeven in 2 years
“It’s definitely been a successful project,” Lockhart concludes. “We’ve been able to meet our target headcount reduction, of approximately 73%, and it’s also led the way for us to explore other AGV possibilities.”
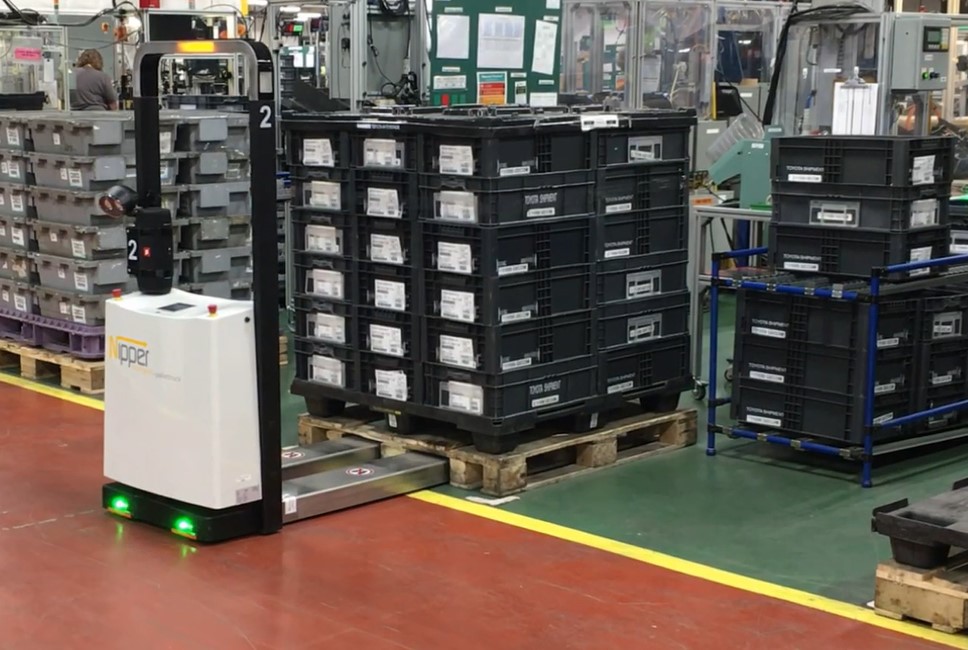
GECOM Corporation's five current warehouse AGVs cover 65 assembly lines, working 24 hours a day, 5 days a week – and the team is open to expanding further.
“It’s definitely been a successful project.”
When calculating breakeven, Lockhart and the team took into account more than just the automated vehicles. “The whole project included the tablets, the AGVs, and the Ignition software. We looked at all that as a whole and calculated how many material handlers could be saved over all three shifts and then calculated an ROI based on that. That’s what we initially presented to management and that’s how we got the go-ahead to move forward.”
GECOM’s Continuous Improvement team usually aim to break even on projects within a year. However, with the automation project, this figure was extended to 24 months. “We were okay with that, as we knew that no matter what customer it was or what assembly line we had running, this AGV deployment was more a general project that would cover pretty much anything we put on the production floor,” Lockhart says.
The next step in the automation process
With its five Nipper AGVs running, and headcount goals achieved, Lockhart and the Continuous Improvement team have already started looking at potential next steps.
This might mean replacing existing manual tuggers with tow truck AGVs or bringing in an automated high reach truck. Whatever the vehicle though, Lockhart is clear it will be ANT driven and ready to slot seamlessly into GECOM’s existing fleet.