The company launched the award-winning multi-year Project Genesis, combining autonomous mobile robots (AMRs) with industrial robots to grow the company, despite its being located in one of the most expensive labor markets in the world.
Automate or relocate
Semiconductors are one of the essentials of modern life, helping run everything from refrigerators to cars, to Bluetooth earbuds. But they are complex to create: materials must be moved through a facility multiple times in variable patterns.
ABB previously relied on manual labor to transport chips and load them into equipment. However, workers in Switzerland are the most expensive in Europe - and even the most well-trained worker will sometimes make mistakes.
“With the higher cost of human resources in Switzerland compared with those in Eastern Europe, management’s choice was becoming increasingly clear: automate or relocate.”
“With the higher cost of human resources in Switzerland compared with those in Eastern Europe, management’s choice was becoming increasingly clear: automate or relocate,” comments Nicola Tomatis, CEO of AMR partner BlueBotics. “Project Genesis was designed in order to keep production at Lenzburg.”
At a glance: ABB’s mobile robot project
Company | ABB Semiconductors |
---|---|
Location | Lenzburg, Switzerland |
Vehicles | 14 mini™ AMRs by BlueBotics |
Industrial robots | IRB 1600 robotic arms by ABB |
Operation system | MOM by ABB |
Before launching Project Genesis at full-scale, a pilot project was rolled out.
Customized, clean-room ready mini™ AMRs by BlueBotics were programmed to work together with ABB’s industrial robotic arms. The AMRs were fitted with lift modules, so they were able to drive under, and then lift and move wheeled racks.
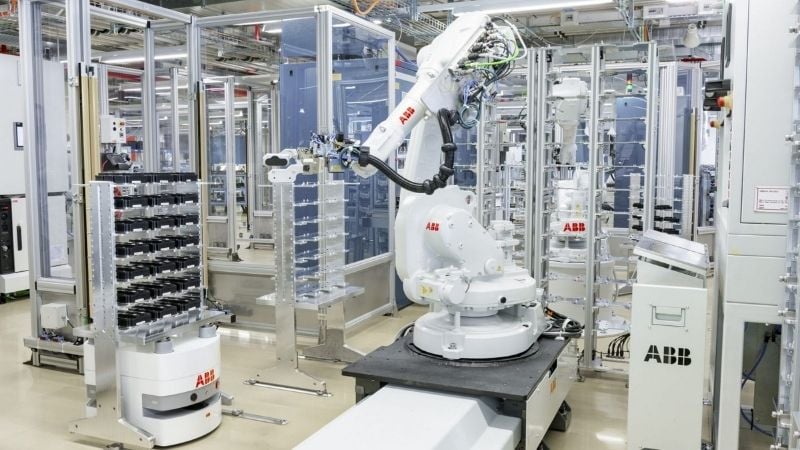
“The experience that we gained from the pilot installation and from cooperation with each of our partners was critical to be able to really implement the entire project,” says David Hajas, ABB’s BiMOS backend automation Program Manager.
“The vision is full automation of the complete production, including transport, logistics and other non-value adding but necessary processes. The complete production will be controlled by one single person,” Hajas continues.
Throughout the pilot project, the factory kept on working. Project Genesis did not excessively restrict the facility’s operation, even as it reimagined it. The fleet of mini™ AMRs seamlessly transferred materials between ABB robots, each capable of producing a wide variety of product types.
“One single person”: MOM
ABB’s automation vision was that one single person could control the entire facility. This was enabled by ABB’s own operations management system, MOM.
With MOM, a single person can communicate with and control every AMR and robot in the facility, determining the next best position for each product – from raw materials to finished items.
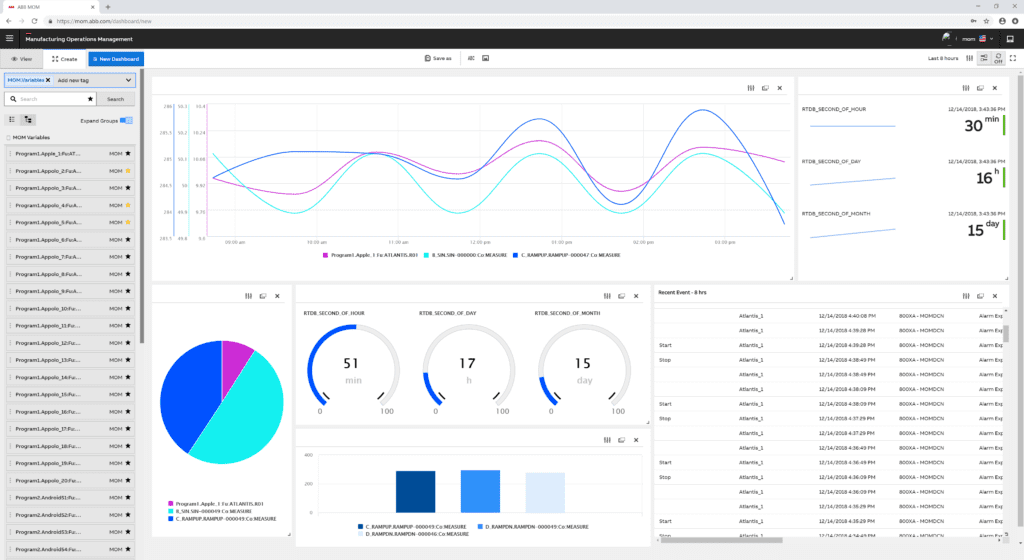
Each automated mobile robot and industrial robot connects to the MOM manufacturing execution software. The mini™ is connected to MOM and the other AMRs in the fleet via ANT server software’s API. ANT driven robots are fleet-ready, and so these vehicles were easy to connect to the MES, and to each other. If needed in future, further ANT driven robots or AGVs could be added seamlessly.
Unlike 20th-century production lines, those powered by MOM are agile, flexible and autonomous. MOM and its robots are able to react instantly to changing conditions, ensuring production continues to run smoothly.
“Our approach, by creating an agile manufacturing environment, has opened some smart thinking and given results never before seen in the discrete manufacturing sector,” says Peter Meier, ABB’s Industry 4.0 Manager.
“Excellent Location Safeguarding by Digitalization”
During the roll-out of this multi-year automation project, ABB Semiconductors was once more recognized as an Industry 4.0 leader, with Lenzburg receiving the prestigious Factory of the Year 2018 award in the category ‘Excellent Location Safeguarding by Digitalization’.
“The main benefits of Genesis are a significant productivity increase, as well as enhancement of the product’s quality. In addition, centralized storage and access to all production data, opens up the way for machine learning and this will help us to be even more competitive in the future,” concludes Hajas.
Having successfully avoided offshoring with the deployment of intelligent automation, ABB can continue to grow its semiconductor operation in its original Swiss location, keeping valuable knowledge, skills and profit within the country.
Since this article was first written, several additional BlueBotics mini™ AMRs have been added to the Lenzburg fleet.