This article is part of a series on how to buy different types of automated guided vehicles and autonomous mobile robots. Also published: how to buy a pallet truck AGV. Also watch: How to buy a tugger AGV (webinar).
When it comes to moving large amounts of parts or stock around a plant or warehouse, manual tow trucks are a well-established solution. However, with driver recruitment often a challenge and managers looking to have existing staff work on higher value tasks, towing is an application ripe for automation. This is where tugger AGVs come in.
We spoke with three leading producers of tugger AGVs (also called tow or tow tractor AGVs) and asked them everything you might need to know when investing in this technology, ranging from how these vehicles move around, common safety concerns, and the payload capacities available, to the potential ROI on offer, and what best practice looks like when planning their deployment. We hope you find it useful.
1. USAGE AND BENEFITS
Per Augustsson (FlexQube): Towing AGVs are most common in industries like manufacturing and production, where materials are moved long distances within factories and warehouses. AGVs are commonly used because they help manufacturers streamline their processes to become more efficient, cost-effective, and to increase safety for operators.
James Jones (MasterMover): Towing or tugging AGVs are used to pull one or more trolleys or carts in a train formation. These types of AGV are synonymous with the automotive and logistics industries because of the repetitive nature of how products are moved from A to B, but in fact they can be used in any industry where towing tractors are currently being used to move loads inside and outside. The design of towing AGVs makes them ideal for industries where the movement of loads are frequent, over long distances, and where multiple drop-offs and pickups are required along a set route.
Jared Sanders (Bastian Solutions): Towing AGVs are mostly used in manufacturing environments due to the capacity and dimensions of the loads involved. Tug AGVs transport very heavy, large payloads across distances, making them ideal for manufacturing processes like assembly line indexing, floor-to-floor transfers, and milk runs. In distribution centers or warehousing applications, we mostly see AGV lifting functions being utilized to interface with racking and other material handling equipment.
“AGVs are ideal for industries where the movement of loads are frequent, over long distances, and where multiple drop-offs and pickups are required along a set route.”
Sanders: Typically, customers are looking to relocate their labor force to processes that provide more value add. At other times, it’s to reduce quality defects, improve safety, or optimize their overall facility.
Augustsson: For sure, efficiency. Towing AGVs can transport many carts at the same time, making it easier to reach a good ROI on your investment.
Jones: Businesses look to automated towing systems to improve their operational efficiency, reduce cycle times and improve the utilization of labor. Their applications are diverse, but typically businesses adopt towing AGVs to automate their existing towing operations, whereby a manual vehicle is used to drive trains of trolleys or carts across long distances. This can be both indoor and outdoor use. This lets businesses free up operators to focus on value-adding or skilled tasks, which are often less suited to automation.
For example, we recently worked with Toyota to roll out towing AGVs for exactly this - to improve their operational efficiency and labor utilization - in the movement of resin backdoors at their factory in Derbyshire, UK. Previously, the driving process was completed using a ride-on tow tractor and a licensed driver. That meant each shift needed dedicated resources for this process. Identifying this as a non-value-adding activity and an area of waste, Toyota decided to investigate automating this process to maximize efficiency.
Jones: A towing AGV ultimately creates a flexible train system. Using a traditional manually driven system requires dedicated resources to carry out what is a low value adding, but essential, process. Using a towing AGV to automate this process frees up staff to work on more productive and fulfilling activities, leaving the repetitive work to the AGV. In the case of our towing AGVs, these can also handle much heavier payloads than traditional tow tractor systems, which means more trolleys or carts can be added to the train; this in turn maximizes efficiency and increases throughput.
Sanders: Tugger AGVs create a consistent, repeatable, and effective way to move material within a facility. They can pull loads at higher capacities, with more product behind the vehicle, than traditional pallet moving equipment like pallet jacks or even other AGVs, which have a 1:1 vehicle-to-load ratio. And in contrast to a conveyor, which is a fixed structure, towing AGVs are very flexible, as they can better adapt to existing and new process flows.
Augustsson: As mentioned, towing is an affordable method of transporting many load carriers at the same time with one single AMR. It gives an improved ROI in comparison to traditional AGVs that only can move one load carrier at a time, which results in more traffic and higher investment costs.
This discussion was continued in our webinar on this topic. Watch it now.
Sanders: Towing vehicles, depending on the form factor, can be used to move many different types of packages or materials. We use tow-type vehicles for moving raw materials, parts, and finished goods into and out of robotic cells, line-side deliveries, or for long runs that require multiple stops for different products.
For example, we worked with DENSO, the second largest automotive parts supplier in the world, to automate the transportation of product pallets from receiving to production lines in their Maryville, Tennessee facility. Previously, this process was operated 90% manually. The biggest concern with automating was safety, as the AGV would need to transport payloads ranging from 4,850 lbs to 10,000 lbs around employees, infrastructure and other product. With five integrated Toyota Core Tow Tractors, DENSO reduced defects, improved productivity and kept 100% of their headcount.
Jones: Within manufacturing, towing AGVs are mostly used in the sideline delivery of components, parts, and equipment to production lines; critical but repetitive supporting tasks. For example, in the automotive industry a towing AGV might interact with transfer systems to create a demand to transfer parts onto a mother and daughter cart system. The AGV would then take a command to transport these to the lineside for assembly, creating a fully touchless intralogistics system that moves loads just-in-time. Then, for heavy plant assembly, tugger AGVs are often used to precisely transfer work-in-progress and sub-assemblies through a staged production process.
Effectively, towing AGVs can be used to streamline any highly repetitive process that involves towing goods from A to B across a site. Their use isn’t limited to the automotive or manufacturing sectors. In logistics environments, they’re increasingly used to improve efficiency by enabling multiple loads to be moved at once. For example, we provided a towing AGV to for a leading 3PL provider as a more efficient and scalable alternative to forklift trucks. Cages were used to transport goods from logistics depots to stores. When these cages were returned to the depot, they were located on the opposite side of the site from where they’re needed for stock fulfilment. Previously, the client had used forklift trucks to move their cages, but they could only move a small number at a time and were traveling in highly congested areas. With a towing AGV, the movement of stock is automated and the AGV can move five times the number of roll cages in one go. So, at this client, forklifts are now only used outside, in safe areas, and fewer operators are needed to transfer stock across the site.
Augustsson: ‘Milk runs’ are probably the most feasible process, meaning some kind of round loop with pre-defined areas for the loading and unloading of material, either by a forklift or manually if it’s totes. Milk runs already have a clear process defined, and this process remains the same when switching from a manual to an automatic towing solution.
Replacing manual tugger trains that performing line-side replenishment in manufacturing environments is more challenging. These trains are normally a “mother/daughter” type, where five or more daughter carts are pulled with a manual tugger. The driver of the train is also responsible for replenishing the carts next to the assembly line. Due to this, an automated tugger solution is less feasible for line-side replenishment because the carts can only be transported to the right location in the transport aisle; they can’t be automatically delivered all the way to the point of use, where the assembler is located. One way to mitigate this is to tow single carts and do reverse or aligned parking at the assembly line, but then the main benefit of towing – moving several carts at the same time – disappears, and there are other types of robots available that are able to move single unit carts.
Augustsson: These processes, if we talk milk runs, were previously performed by manual tuggers, which is a good thing when automating because it means the process flow is already defined.
Jones: Typically, towing AGVs are used to replace ride-on towing tractors, or in situations where loads were previously static (i.e., on a pallet) and are now dynamic (part of a train system using carts or dollies). In both manufacturing and logistics, there are typically multiple shifts running per day, which means multiple operators are needed to drive manual tow tractors each day. When towing tractors are used to transport trains of dollies or carts through a facility, this often involves multiple stops for loading, unloading and transfers, which can be time-consuming for operators. So, the repetitive and predictable nature of these processes makes them ideal for automation. In this particular application, businesses can typically see return on investment in less than 1.5 years through the reallocation of labor, increased efficiency, and reduced cycle times across multiple shifts.
“Towing enables the transportation of many carts at the same time, making it easier to reach a good ROI on your investment.”
Sanders: In some cases, these moves would be made with traditional, manually driven forklifts or tuggers. As mentioned, this method requires dedicated human resources and may force processes to run consecutively, rather than concurrently. Other cases would have used another form of automation such as a conveyor. And while there are many benefits to conveyor systems, their static designs don’t lend to operational flexibility the way AGV solutions do, as tug AGVs can accommodate floor plan restrictions, improve egress, and redeploy to other processes or other areas of the facility.
2. HOW TUGGER AGVs WORK
Sanders: Many different payloads. It depends on which type of vehicle is being used and how many carts are being tugged at one time. Payload dimensions and weights need to be evaluated to determine which model is best suited to each application. Our tugging AGVs, for example, are capable of moving payloads of 4,500 pounds (2,041 kg) with a small mouse-type vehicle, such as our M10, or 10,000 pounds (4,346 kg) with the Toyota 8TB50A.
Augustsson: This is different for every use case. The FlexQube system, which consists of one robot that couples with an eco-system of different load carriers, is applicable to a variety of payloads. Common loads are pallets, racks, material kits and totes, for applications where automation is feasible. The typical payload capacity we see mostly needed is between 2,000 and 3,000 kg, however, our tugger AGV can handle a payload of 4,000 kg.
“Previously, forklift trucks were used to move cages, but could only move a small number at a time and were traveling in highly congested areas. With a towing AGV, the movement of stock is automated, and the AGV can move five times the number of roll cages in one go.”
James: This is very much dependent on the design and capability of the base vehicle. Our MasterTow AGVs can handle up to 20,000 kg, while other tuggers in our range offer capacities of up to 70,000 kg. Within the automotive industry, trolley train systems often weigh around 2,000 kg, whereas within heavy plant, aerospace and other industrial manufacturing industries loads can easily weigh in excess of 10,000 kg.
Sanders: At Bastian, we use either an electric, spring-loaded towing pin, for smaller vehicle types such as our ANT driven M10 and ML2. For the Toyota 8TB50A, we use many different customer hitches to connect the tugger to the dolly train in service.
Any vehicle using a towing pin can be considered an automated option. These models automatically pin up or down to pick or drop loads/carts throughout a facility. In some applications, the automated pin up/down function is not utilized though, and we can tether the AGV and cart together for additional functionality that requires control logic. Many of our tow AGV offerings are designed for automated coupling/connecting, to increase the autonomy of the vehicles as well as the efficiency of the overall AGV system. In any tugging application, it’s important to consider overall system performance and functionality when selecting the correct vehicle model and designing the system.
Augustsson: Our towing AGV, which we call the Navigator AMR, is unique in the market with a standardized and patented coupling that can automatically couple and uncouple from a full train set. The system is based on a modular 'one robot/multi-carrier' concept, where the AMR itself is a non-load carrying system - equipped with a navigation system, safety system and battery - which couples with the motorized load carrier.
Jones: This is very much customer driven. In our 25-plus years of designing pedestrian and remote-controlled electric tugs and tows, we’ve found it depends on several factors. The most basic method of connecting or hitching to a load is manual, where an operator hooks the AGV up to a cart or trolley. This is typically a simple towing pin, though sometimes other options like ball hitches are used depending on the interface of the trolley.
The next option is where the AGV and trolley train remain connected throughout the operation. For example, if an AGV is used to tow the same train of trolleys all day, every day, then regular coupling and uncoupling isn’t required. The most advanced — a system we’ve installed for a number of customers who frequently handle higher volumes of carts — is auto-coupling. This is where the connection to trolleys is completely touchless, with no operator involvement. This type of system involves the AGV autonomously reversing and connecting to the next trolley system. The AGV takes its command from the fleet management software to determine the required trolley train, connect to it, deliver it to the production line, and drop it off. From there, the AGV then autonomously disconnects from the trolley system and collects an empty trolley train, returning it back to the loading area for replenishment.
Augustsson: At FlexQube we offer AGV and AMR models based on either natural feature navigation or line following. The choice of navigation really depends on the complexity of the route. The more complex the layout, the more feasible natural feature navigation becomes.
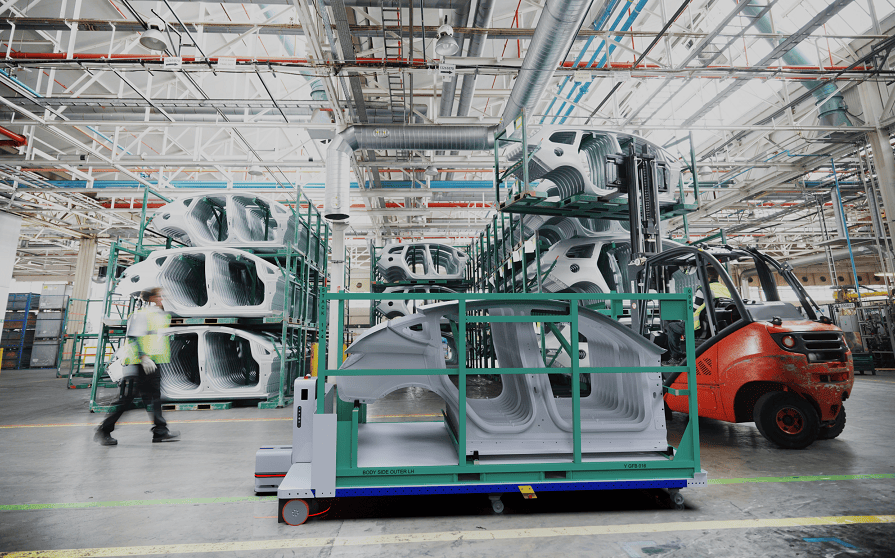
Jones: Natural feature navigation is a faster, more flexible solution that enables an AGV to follow a virtual predefined path. It’s easy to adapt and install, and there are no infrastructure adjustments required. A simpler and more budget-friendly form of AGV navigation technology is line following navigation, whereby vehicles follow a physical predefined path; as the name suggests, they follow a line on the floor. Installation of these vehicles is typically slower, as a physical line needs to be installed and, critically for the AGV to work effectively, this line needs to be maintained.
Sanders: It’s really model dependent. Our tug AGVs use either magnetic tape or natural feature navigation from BlueBotics. Magnetic guidance has been in the market since the 1980s and is easily accepted within customer facilities thanks to its longevity and reliability. It provides a clearly marked path where the AGV will be traveling and doesn’t rely on environmental landmarks for navigation. Essentially, it will ignore the moving environment outside the vehicle’s pathway. Natural feature technology generally makes for a quicker deployment process and gives the user greater flexibility after implementation. Vehicles do rely on physical landmarks or reflectors to navigate a facility, but this technology doesn’t require as much infrastructure as other navigation types.
Jones: A towing AGV presents some unique challenges when compared to other types of more basic AGVs. Alongside safety features such as integrated Emergency Stop systems and adaptive safety fields, the most effective way to ensure the safe movement of mother and daughter carts is by carefully evaluating the application. It’s important to consider the specifics of the trolley system, the route, and the overall environment, plus the weight of the load being moved, the speed requirements and, crucially, the braking distances and turning radius needed.
Augustsson: Safety can be a concern since tuggers do not have safety fields that cover all the carts behind. Collisions can be avoided though by adding extra sensors on the daughter carts, and our AMR supports this add-on through the standardized coupling.
Sanders: Safety fields can be triggered based on the vehicle’s velocity or called on command at specific locations along the travel path. At Bastian we evaluate all payload widths and validate each safety field to cover the maximum width possible. If a tugger will move payloads of varying widths, we may need an operator input to confirm which safety fields should be used. In most daughter cart applications, we also use other devices, other technologies, between each dolly. These might include leading edge safety bumpers, SICK Scan Grid technology, or a physical barrier.
Additionally, we use a combination of BlueBotics’ ANT navigation software and our proprietary AV software to manage traffic control functions in certain areas. This could include bi-directional pathways, buffering stations, or physical spaces that don’t adhere to the ITSDF B56.5 standards.
Sanders: Tugger AGVs can work seamlessly with other automated and manual traffic. The key to success is to select the correct vehicle and navigation type, and the right overall application or system design. If the wrong vehicle or navigation is selected, or if it’s not well integrated into the environment, the vehicle or system might not be successful. Our integrated AGVs use proprietary middleware to seamlessly connect vehicles from various manufacturers to customers’ enterprise systems. With this pre-packaged software stack, users can orchestrate complex, multi-fleet systems, improving safety, visibility and interoperability.
Jones: A fleet management system enables the AGV to communicate and interact with existing automated vehicles or infrastructure — like shutter doors and traffic light systems — to ensure a safe and programmed response. For manually driven vehicles such as forklifts, good site discipline and experience mean drivers quickly adapt to the repeatable and predictable way AGVs operate. Alongside this, towing AGVs also boast impressive safety features, so that they stop if their path is blocked or congested by other vehicles.
Augustsson: With advanced safety systems and an advanced fleet management system, the tugger AGV can respond to its environment and the traffic around it to ensure it delivers materials to the right place, at the right time, in a safe manner. If there are obstacles that interfere with its route, the safety system triggers the AGV to slow down or stop until the object is removed to ensure high safety for other traffic and operators.
Jones: Yes, and we’ve installed these systems very successfully. We were recently asked to demonstrate our AGV, for example, on an application where an outdoor AGV was required to navigate from inside a bottling facility, through a shutter door, down a slope, across a busy distribution yard, and into a warehouse. We’ve also installed an outdoor AGV system to move loads from building to building at another automotive manufacturing site, where the AGV needed to be able to handle the typically wet British weather without issues.
Sanders: Yes, there are towing AGVs on the market that can go outdoors. Our vehicles are designed for indoor use, but they can transport materials between buildings through corridors.
Augustsson: Typically, yes, but we do not offer this, and it is not included in our roadmap.
This discussion was continued in our webinar on this topic. Watch it now.
Augustsson: This can be important for some use cases and can also work as a backup, in case of deviating routes that need managing at short notice, or if an obstacle must be passed. Our focus at FlexQube though is to offer a fully automated towing solution, which includes automatic coupling and uncoupling of the train set. Our AMR system is designed with automation in mind and isn’t built upon the retrofitting of manual tow tractors. This gives us the possibility to optimize the system’s design, reliability and performance. Manual driving is still possible with a joystick when a situation requires, but this is not intended to be part of the daily process, only in exceptional cases.
“AGVs, in particular towing AGVs, are a great way to begin your automation journey by focusing on simple, repetitive operations.”
Sanders: The ability to switch from automated to manual operation is often critical to a customer’s decision-making process, as going manual provides them with a built-in backup process, or it can allow operators to catch up if the overall operation is behind.
Additionally, there are applications where a percentage of the vehicle’s process needs to be manual, such as unhitching an empty daughter train and selecting from a multitude of full daughter trains. Building in this redundancy or flexibility helps the customer better support their operations.
Jones: AGVs are there to autonomously navigate, but the ability to switch between automated and manual modes does act as a very useful safety-net or contingency. For example, if an AGV’s route is blocked and the obstruction can’t be quickly cleared, the ability to manually intervene and move the vehicle means that operations can remain fluid, avoiding bottlenecks. Likewise, the ability to manually operate the AGV is useful if there’s a manual battery change process or maintenance is required on the vehicle.
3. INTEGRATION
Jones: When a towing operation is manual, a trained driver needs to use their intuition to adapt their driving style and ensure it’s safe to turn left, right, or to stop the train. When automating this movement, it’s important then that the route, load and safety requirements are carefully considered in the same way, to ensure the AGV delivers the correct, programmed response in every situation. The trolley train must snake behind the AGV, ensuring it follows the center of the AGV and a safe path. Unlike a unit load or underride AGV, a 360-degree safety scanner cannot be fixed to cover every trolley and angle, so the correct trolley set-up and safety systems are crucial. For example, a chain of Emergency Stop systems can be fitted to the trolleys to make sure the train can be immediately stopped from any part of the system. AGVs can also be programmed with a set-off safety delay, to delay the start of the movement by a preset time, giving operators time to get well clear of the rear of the train. Adaptive safety systems can also be integrated to ensure safe transport along the route.
Sanders: We have to consider many different application aspects, but the key variables are vehicle type, floor conditions, load dimensions and weight, maximum and constant drawbar values, and endpoint processes. These considerations affect the vehicle’s form factor, load handling device, controls, and integration.
Augustsson: You need to consider the routes, so you have enough space and optimized tracking for the carts in the train to manage curves and follow the AGV’s path. You also need to consider how material will be loaded and unloaded onto the carts, since this will require a manual process. If not, rollers can be used.
James: This ultimately depends on the capability of the base vehicle. Our towing AGVs can drive autonomously indoors, outdoors, up slopes and on rough terrain.
Sanders: At Bastian, we evaluate the environmental conditions of all our AGV applications. For towing in particular, environmental conditions like – but not limited to – floor undulation, drive wheel friction, floor fluids, and floor grades all need to be evaluated. Specific models of AGV, such as our 3A or M10, would need us to review floor conditions more carefully, because these vehicles have low ground clearance.
Augustsson: I’d say that in terms of floor quality, towing is a more forgiving method of moving material, but it does require careful consideration of the routes the AGV will use, since it can’t reverse with its load.
Jones: The best approach is to keep it simple. Focus on proving the concept and capability, and then progress to a full AGV rollout. For example, if the end goal is a fully touchless and autonomous transfer system, there will typically be two phases: initially, we’ll install an automated transfer system between a trolley train and the production equipment, and then introduce an AGV as part of the process. This staged approach often gets to the end goal much quicker and it ensures the process is fully defined before we integrate the AGV itself.
The second crucial point is to work closely with the customer. We spend lots of time exploring exactly what our customers are looking to achieve with automation — today and tomorrow — so that we can ensure any solution they invest in is the right one for them.
Sanders: The integration of autonomous vehicles should be discussed at all levels of your company to overcome any concerns staff have and to answer questions about this technology. This will help with overall acceptance and improve how the AGVs are used.
Generally, an automated tugger can execute most movements that a manual tugger can make. It’s best to examine your current processes carefully and determine where an operator makes manual adjustments while driving. Understanding these small nuances about the vehicle’s route will better prepare the implementation team and improve how they integrate the fleet.
Augustsson: The best practice is probably to automate routes that are already served by manual tuggers today, meaning those used for moving lots of material a long distance.
4. SUPPORT & MAINTENANCE
Sanders: Tugger maintenance is relatively low. Most components are electronic, so they don’t need much maintenance but moving parts, such as wheels and bearings, may need to be repaired or replaced on occasion. With regular preventative maintenance, typical tugger systems can last 7-10 years after initial integration and deployment.
Augustsson: Maintenance for tugger AGVs typically involves preventative measures to ensure their longevity, most often related to wear and tear of the motor wheels and towbar.
Jones: A well-designed and correctly specified AGV system will outperform manually driven vehicles and require minimal maintenance. But, as with any piece of industrial equipment, regular maintenance is crucial.
Weekly checks should involve keeping scanner lenses clean and free from debris or dirt, while high-wear components such as drive wheels, tires and castors should be checked on a quarterly basis. Data capture and telematics systems can be incredibly valuable, enabling preventative maintenance and ensuring optimum performance. These can provide insights by monitoring motor temperature and battery performance, helping identify potential issues before they arise.
Augustsson: We provide on-site training and support so the customer can take full ownership of the system if they want.
Jones: We provide full installation of all our AGVs to ensure the system is up and running. We’re also on-hand for on-site and remote technical support for the lifetime of the product.
Jones: We provide full installation of all our AGVs to ensure the system is up and running. We’re also on-hand for on-site and remote technical support for the lifetime of the product.
Sanders: We provide operator, technical and programming trainings, and access to our learning management system for reference and supplemental content. We host training sessions at our Georgetown, Kentucky facility to give customers hands-on experience, as we’ve found bringing them to our site for training provides the best end results. We support customers on-site for installation and go-live.
5. INVESTING IN TUGGER AGVs
Augustsson: There are several factors to consider, such as payload capacity, flexibility and versatility, a vehicle’s navigation system, and its safety features. It’s important to make an informed decision that aligns with your operational requirements and business objectives.
Jones: Safety is non–negotiable for every piece of equipment, autonomous or not, so it’s crucial that any AGV system is fitted out with safety features such as Emergency Stop systems and adaptive speed settings, along with any specific systems needed to safely interact on your site. Secondly, a proven vehicle design is essential. Afterall, an AGV still needs the core capability to move a load day in, day out. Vehicles with heavier tugging capabilities are typically more durable, so they’re better suited to intensive operations and last longer. They also have superior braking capabilities.
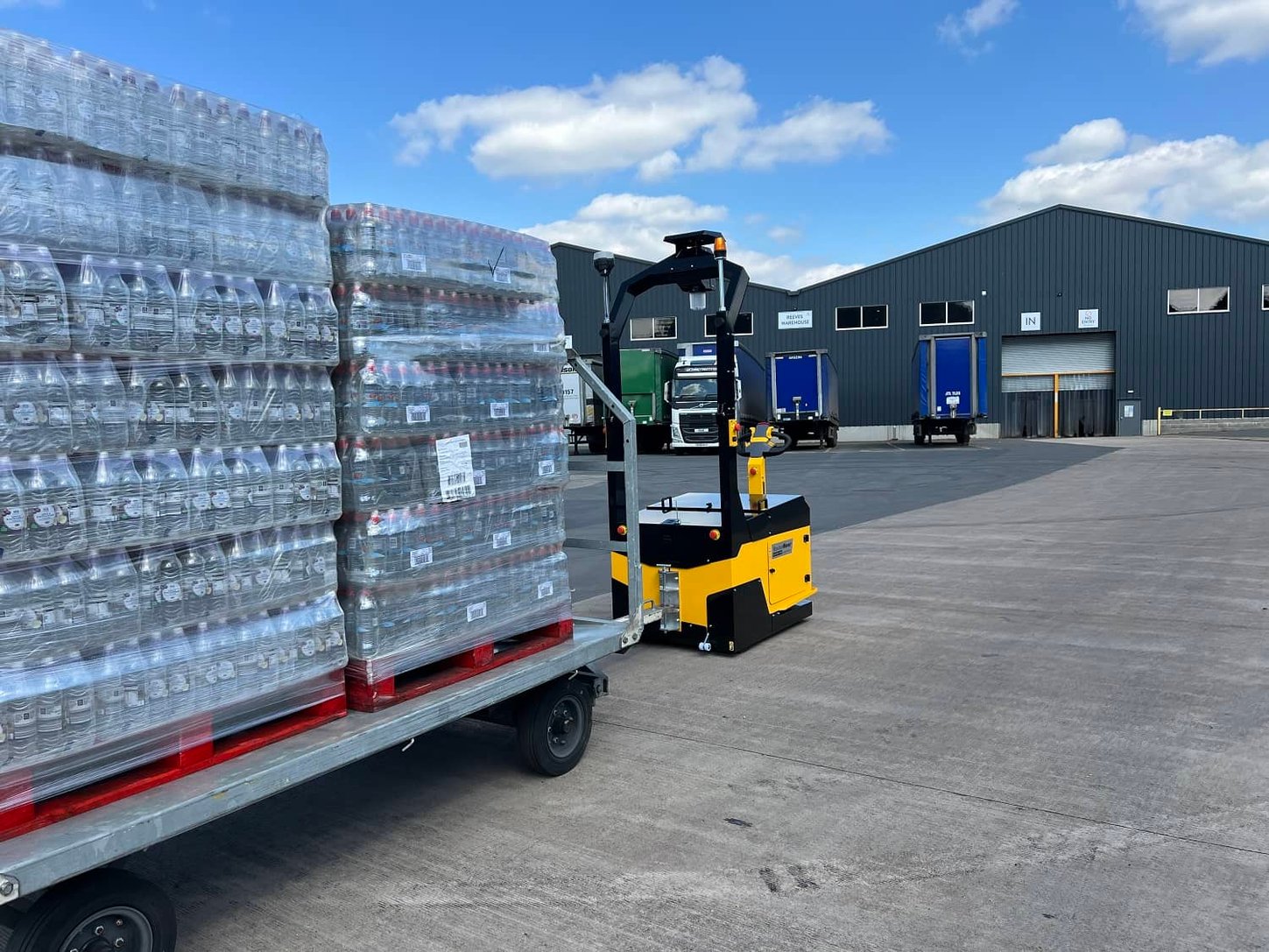
Another consideration is an AGV’s reliability and simplicity. This ties in with vehicle design, as well as the reliability of a system’s navigation technology. Lastly, the biggest stumbling block of automation projects is that they start off too complex. AGVs, in particular towing AGVs, are a great way to begin your automation journey by focusing on simple, repetitive operations.
Sanders: When considering a tow type AGV, a customer should think through these questions: Do my current or future processes support a tugger type vehicle? How will the product or packaging be placed or removed from the daughter train? Are my floor conditions (ramps, undulation, cracks, etc.) conducive to a tugger? Have I communicated this potential equipment change to all affected levels of our organization?
Sanders: Most customers can expect a return on their investment within 18 to 24 months. Each customer's return will be slightly different based on their application and ROI calculation. Additionally, customers will typically see gains in flexibility, total cost of ownership, quality, safety and other means.
Jones: AGVs offer a significant return on investment, with potential savings depending on the operational shift structure, investment cost, and process. For single-shift operations, the ROI ranges from 50% over three years to 150% over five years. This increases dramatically in multi-shift scenarios, with double shifts achieving a 200% ROI over three years and 399% over five, and triple shifts achieving a 349% ROI over three years and 649% over five years.
This ROI is driven by the reduction in costs associated with using AGVs versus traditional single operator and vehicle setups, where the costs rise steeply over time. Another factor to consider when it comes to ROI is the added benefit of freeing up labor to work on more productive and value-adding tasks.
Augustsson: From an ROI perspective towing is a very beneficial user case, since you can tow multiple carts at the same time. Given the right use case, and running two or more shifts, we can see ROI numbers as low as 12-15 months. Average ROI is likely around 24 months, which is acceptable for most customers given the increased level of safety, flexibility and efficiency tuggers bring.
Ready to talk tugger AGVs?
Take a deeper dive into this topic in our webinar. Are you interested in automating your business' manual towing processes? If so, click here to browse ANT driven tugger AGVs, or contact our expert team to book a free consultation.