In this article, we highlight the three key mistakes to avoid when investing in AGV technology.
Mistake 1: Automating a manual process ‘as is’
AGVs or other mobile robots can only do as they are programmed. If you haven't considered it, a robot cannot deal with it. This means tasks that would take only a minute for a human - such as moving a box that someone left in an aisle, or double-checking with a colleague before packing a rack - can cause an AGV operation to grind to an inefficient halt.
That’s why human-driven, manual processes can often not simply be automated ‘as is’. Instead, a process likely needs to be analyzed, simplified, and standardized before automating.
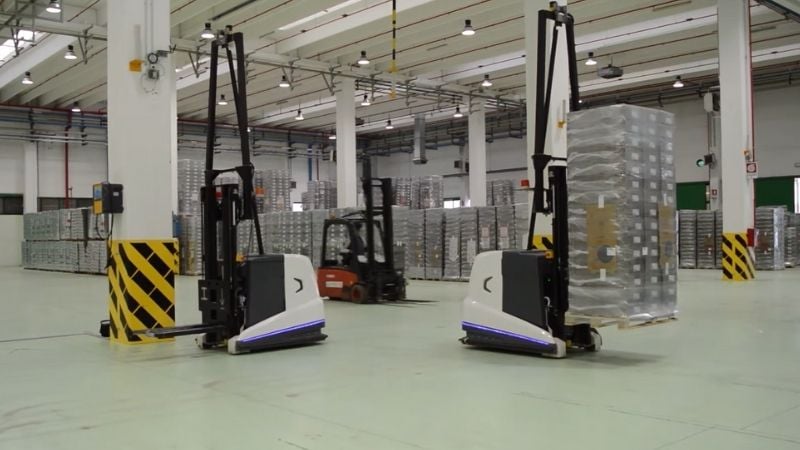
Do this instead: simplify before automating
Follow your existing processes from end to end. Imagine explaining them to a five-year-old (or a robot). Break them down into small, individual steps, and eliminate everything that isn’t essential.
One US company, GECOM Corporation, prepared its installation of F3 Nipper AGVs by asking staff to perform the full range of proposed automated processes using manual tow tractors first. Once these processes had been assessed and fine-tuned, the robots were simply slotted in place of the humans. Read the full case study.
Mistake 2: Don’t assume all AGV navigation systems are the same
AGV systems employ a wide range of different autonomous navigation technologies. Understanding the key differences between these technologies will ensure you select an automated guided vehicle that is reliable, accurate, and suits your company's application.
For example, AGVs that follow a physical line on the floor – such as magnetic tape or inductive wires – are highly accurate, as well as simple to understand and operate. However, they are relatively inflexible: their installation can take time (and money), their routes can become damaged are not quick to modify, plus these systems are inherently limited when it comes to operating a fleet and managing traffic.
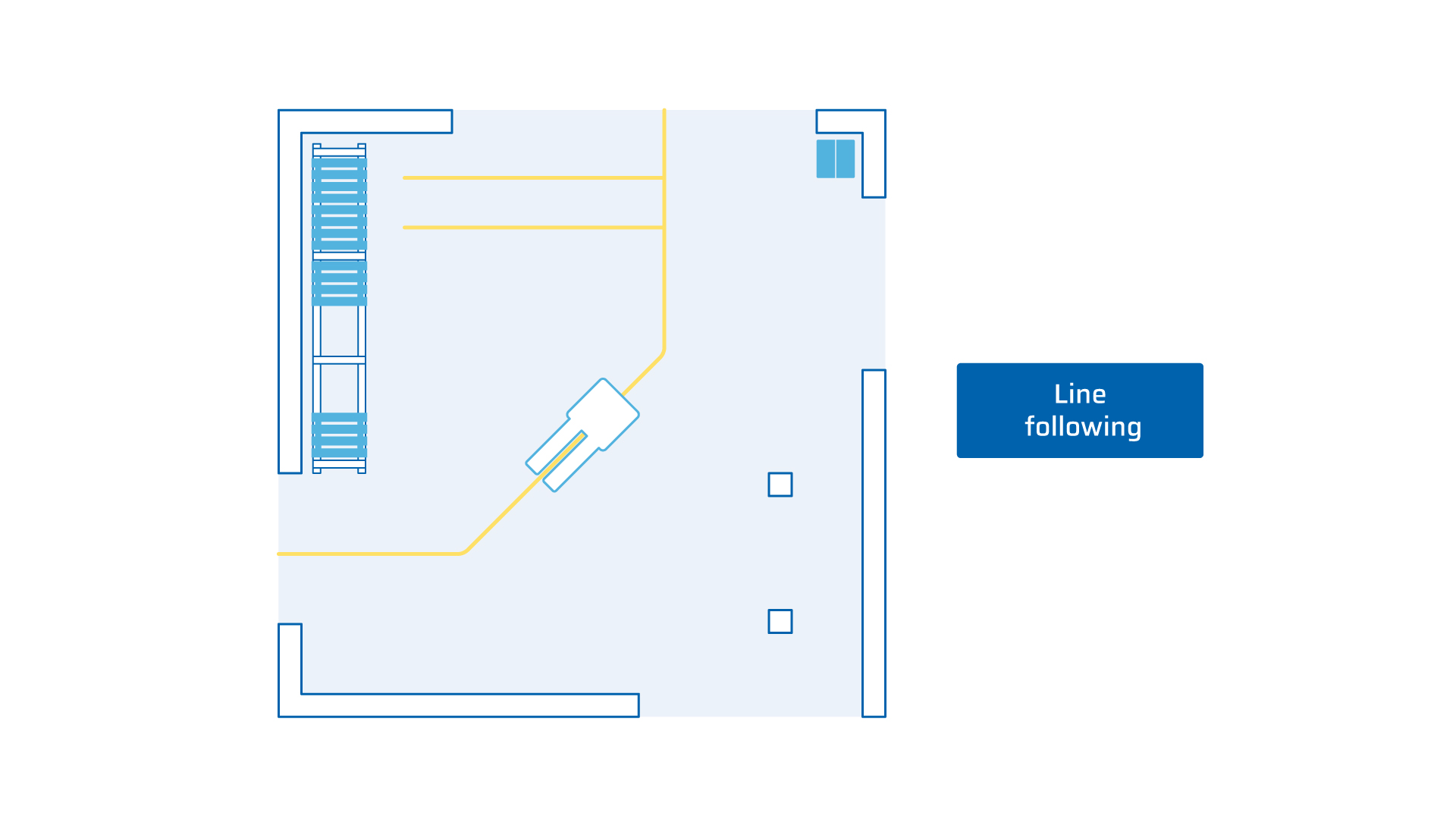
If the process you are looking to automate is simple, such as a single-loop production line, a line following AGV may be perfect for the job. But if your processes are more complex, or your operation may need regularly modifying to adapt to an evolving site, other, more modern navigation technologies could be a better choice.
Laser triangulation is one such approach, but this requires significant installation time and therefore cost.
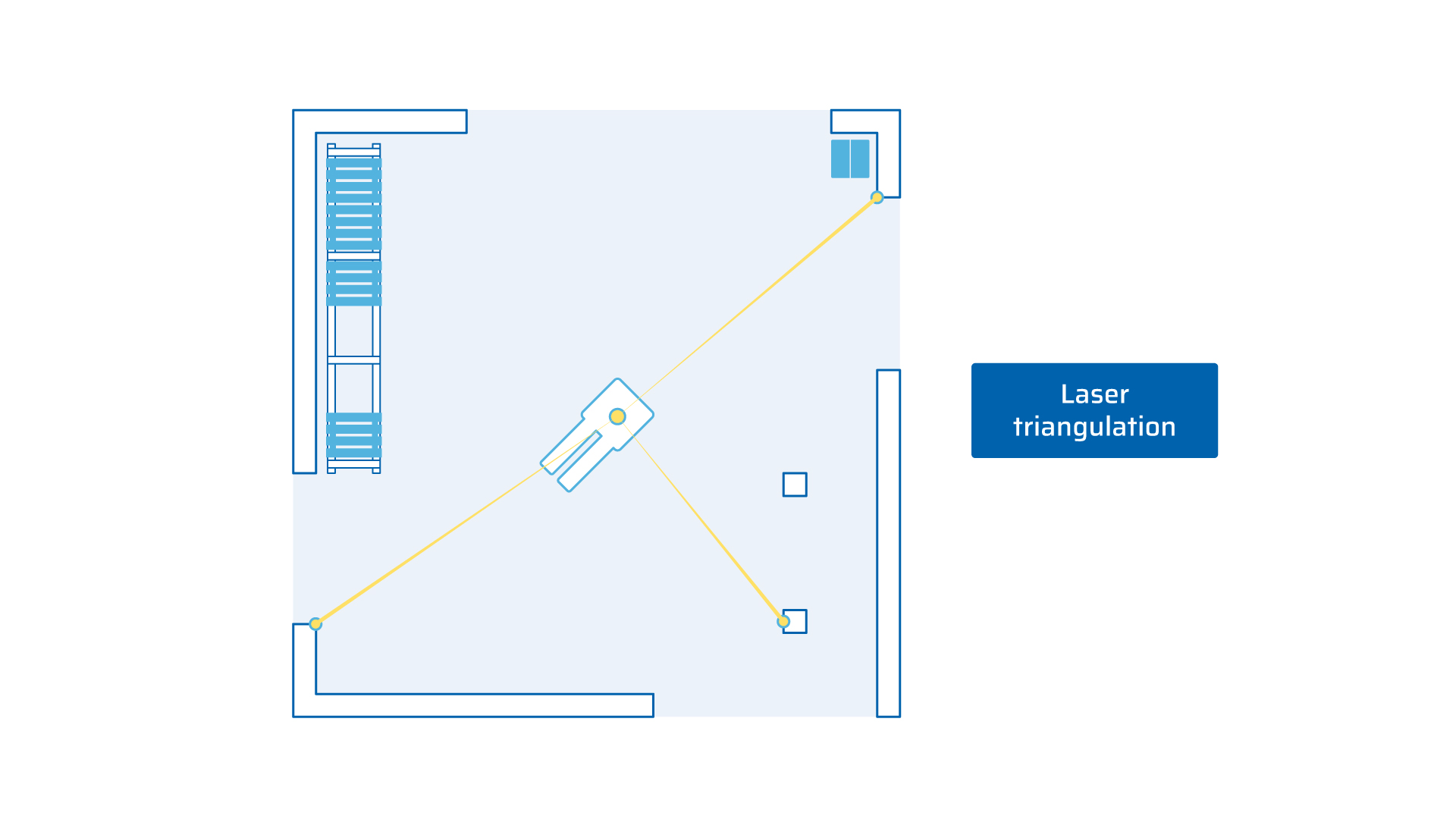
For a solid balance of quick installation, high accuracy and fleet-friendly scalability, we recommend AGV systems driven by natural navigation (such as ANT natural feature navigation).
Plus, it’s possible for vehicles powered by ANT natural feature navigation to accurately navigate outdoors with the product extension ANT everywhere.
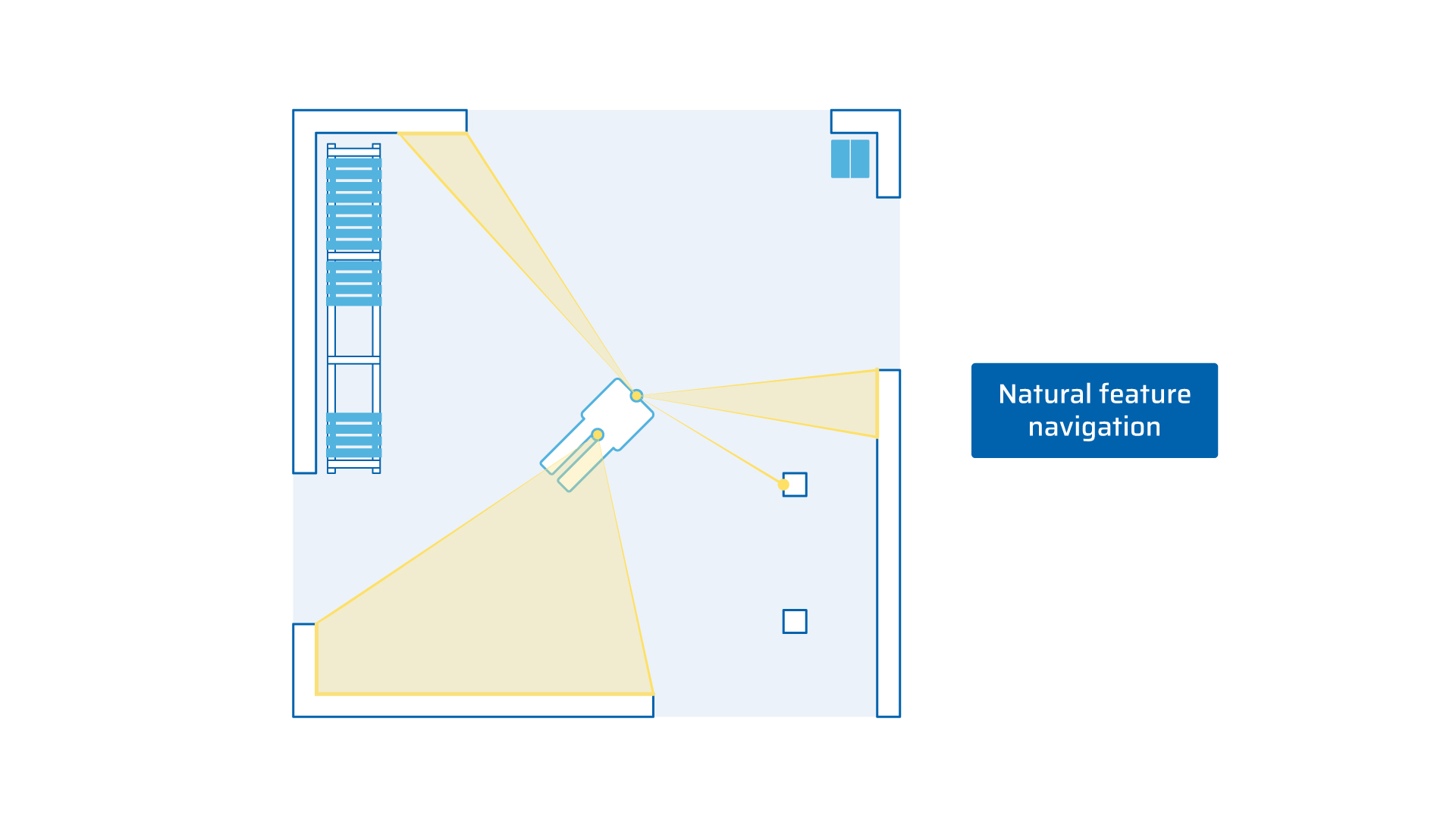
Do this instead: research navigation systems
The navigation system that drives an AGV will have a large impact on its performance and therefore the success of your automation project. Therefore, make sure you fully understand the pros and cons of the different technologies on offer.
Mistake 3: Don’t assume robustness and accuracy
The number of AGV suppliers in the market has increased exponentially in recent years. However, a significant portion of these new manufacturers' systems falls short in terms of the robustness and accuracy they can achieve.
What does this mean for your investment?
Material handling applications usually require a decent level of both accuracy (around 1 cm or a half-inch is usually more than enough) and flexibility (in terms of being able to update routes and vehicle actions easily).
If your AGV’s positioning accuracy is weak, some basic applications may work but many typical logistics applications will simply not be possible.
If, for example, your application requires the picking and dropping of payloads, or if an AGV must move under racks or trollies to pick these up, solid positioning accuracy will be vital. Your AGV system will also need a certain level of accuracy to dock correctly with automatic charging stations, allowing fully autonomous operation (otherwise you might need to add an additional line following piece at such key locations in order to achieve the accuracy required).
Bear in mind that the vehicle accuracy you require must also be highly repeatable. Certainly don't place all your trust in a supplier's all-singing, all-dancing demonstration at their facility. There are plenty of horror stories in the industry about AGV or AMR demos looking great but then - once paid for - these technologies falling well short in real-life commercial use.
Do this instead: check the references
Before working with a vehicle supplier, check how long the company has been in business and how many vehicles they have in operation, today, at client sites.
It may not be possible to speak to another customer (although that would be ideal), but a supplier should supply several references and case studies. Or at the very least a list of client names relevant to your industry.
A version of this article was originally published on MHI.org.